Technology and Applications of rust laser removal machine
Technology and Applications of Rust Laser Removal Machines
Rust laser removal machines utilize advanced laser technology to clean and restore metal surfaces by removing rust, paint, and other contaminants. The core technology involves high-energy laser beams that are precisely controlled to ablate the rust layer without damaging the underlying metal. This process, known as laser ablation, employs pulsed or continuous-wave lasers, typically in the fiber or CO2 variety, with wavelengths optimized for metal surface treatment.
Key Features:
1. Precision and Control: Laser parameters such as pulse duration, energy, and repetition rate can be finely tuned, allowing for selective removal of rust without harming the base material.
2. Non-contact Process: The laser beam does not physically touch the surface, reducing wear and tear on equipment and preventing secondary contamination.
3. Environmental Benefits: Unlike traditional methods, laser cleaning requires no chemicals, produces minimal waste, and is often safer for operators.
Applications:
1. Industrial Maintenance: Rust laser removal is widely used in industries like automotive, aerospace, and manufacturing for maintenance and refurbishment of machinery, tools, and metal parts.
2. Heritage Conservation: It is employed in the restoration of historical artifacts and monuments, where precision and non-destructive cleaning are critical.
3. Pre-Welding and Coating: Preparing metal surfaces by removing rust and contaminants ensures better adhesion and quality in welding and coating processes.
4. Maritime and Offshore: The marine industry uses rust laser removal for the maintenance of ships and offshore structures, combating the persistent issue of rust in harsh sea environments.
Advantages:
– Efficiency: Faster and more efficient compared to mechanical or chemical methods.
– Safety: Reduced risk of exposure to hazardous chemicals and improved workplace safety.
– Cost-Effective: Lower maintenance and operational costs due to the longevity of laser equipment and minimal consumables.
In summary, rust laser removal machines represent a modern, efficient, and environmentally friendly solution for cleaning and restoring metal surfaces across various industries. Their precision, control, and versatility make them an essential tool in industrial maintenance, heritage conservation, and beyond.
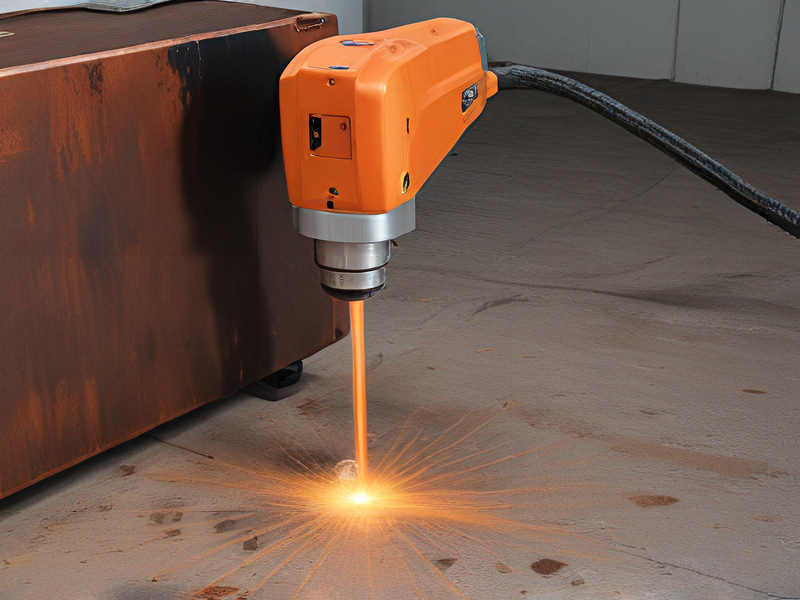
Quality Testing Methods for rust laser removal machine and how to control quality
Quality testing methods for a rust laser removal machine typically involve several key steps to ensure performance and reliability. Here’s an outline on how to control quality:
1. Initial Inspection: Conduct visual and functional checks on components upon arrival to ensure they meet specifications.
2. Functional Testing: Verify that the laser removal machine operates according to design parameters. Test functionality such as power output, laser beam quality, and cooling system efficiency.
3. Material Compatibility: Test the machine on various types of rusted materials to ensure effectiveness across different surfaces.
4. Durability Testing: Perform stress tests to evaluate the machine’s durability under normal and extreme conditions.
5. Safety Checks: Ensure the machine complies with safety standards for laser devices, including emission levels and protective measures.
6. Accuracy and Precision: Use calibrated measurement tools to verify the accuracy and precision of laser targeting and rust removal depth.
7. User Interface Testing: Evaluate the user interface for ease of operation and clarity of instructions.
8. Quality Control Documentation: Maintain detailed records of all testing phases and results for traceability and future reference.
Implementing these quality testing methods helps ensure that the rust laser removal machine meets high standards of performance, reliability, and safety, ultimately enhancing customer satisfaction and product reputation.
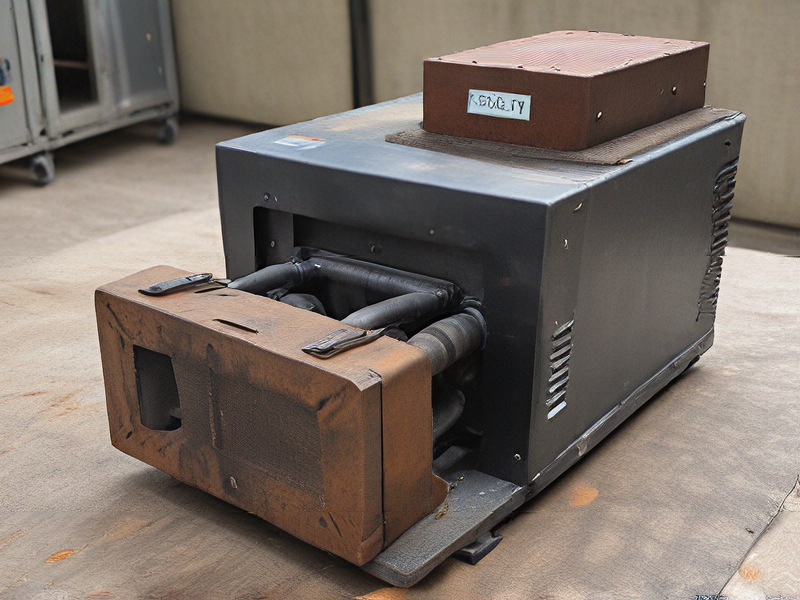
Tips for Procurement and Considerations when Purchasing from rust laser removal machine
When procuring a rust laser removal machine, several tips and considerations can ensure you make a well-informed purchase:
1. Understand Your Needs: Assess the scale of your rust removal tasks. Determine whether a portable or stationary machine suits your needs based on the size and frequency of the jobs.
2. Power and Efficiency: Check the laser’s power output and efficiency. Higher power lasers can remove rust faster but may be more expensive and require more maintenance.
3. Material Compatibility: Ensure the machine can handle the materials you need to clean. Different lasers may be more effective on various metals and surfaces.
4. Precision and Control: Look for machines with adjustable settings for precision. The ability to control the laser’s intensity, pulse, and focus can prevent damage to the underlying material.
5. Safety Features: Rust removal lasers can be dangerous if not handled properly. Ensure the machine has adequate safety features, such as protective enclosures, interlock systems, and emergency shut-off options.
6. Training and Support: Consider the availability of training for operating the machine. Manufacturers offering comprehensive training and robust customer support can be valuable.
7. Maintenance and Longevity: Evaluate the machine’s maintenance requirements and overall durability. Machines with lower maintenance needs and longer lifespans can provide better value over time.
8. Cost: Factor in not only the purchase price but also the cost of operation and maintenance. High-quality machines may have higher upfront costs but lower long-term expenses.
9. Supplier Reputation: Research the reputation of the supplier or manufacturer. Look for reviews, case studies, and customer testimonials to gauge reliability and service quality.
10. Warranty and Service Agreements: A good warranty and service agreement can save costs and downtime. Ensure you understand the terms and coverage.
By considering these factors, you can select a rust laser removal machine that meets your operational needs while providing efficiency and safety.
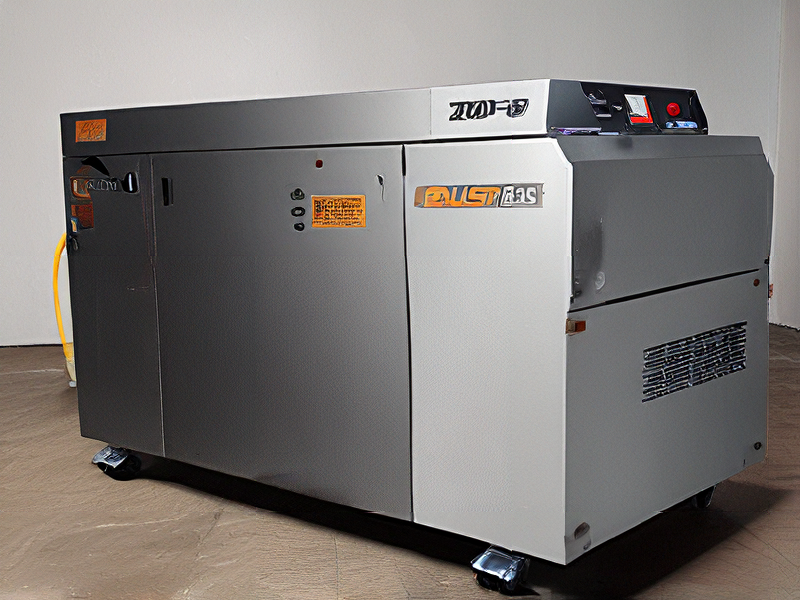
FAQs on Sourcing and Manufacturing from rust laser removal machine in China
FAQs on Sourcing and Manufacturing Rust Laser Removal Machines in China
1. Why source rust laser removal machines from China?
China is a leading manufacturer of industrial equipment, offering cost-effective solutions, advanced technology, and a wide range of options. Manufacturers in China often provide competitive pricing without compromising quality.
2. How to identify reliable suppliers?
Use platforms like Alibaba, Made-in-China, and Global Sources to find suppliers. Look for verified suppliers, read reviews, and check their trade history. Visiting the factory or requesting a video tour can also help ensure reliability.
3. What certifications should the machines have?
Ensure the machines have necessary certifications such as CE (for European markets), ISO, and RoHS. These certifications indicate compliance with international standards.
4. What are the common payment terms?
Common payment terms include 30% deposit before production and 70% balance before shipment. Letter of Credit (L/C) and Trade Assurance through Alibaba are also secure options.
5. How to handle quality control?
Implement strict quality control measures by conducting pre-shipment inspections. Third-party inspection agencies like SGS, Bureau Veritas, and Intertek can provide unbiased quality assessments.
6. What about warranty and after-sales service?
Check the warranty terms provided by the manufacturer, typically ranging from 1 to 3 years. Ensure they offer reliable after-sales service and technical support, which can be crucial for maintenance and troubleshooting.
7. How to manage logistics and shipping?
Work with experienced freight forwarders to handle logistics and shipping. They can assist with customs clearance, documentation, and ensure timely delivery. Consider Incoterms like FOB, CIF, or DDP to understand responsibilities and costs.
8. Are there any import restrictions?
Research and comply with your country’s import regulations and restrictions. Some countries may require specific documentation or have restrictions on importing certain types of machinery.
9. How to negotiate the best deal?
Negotiate based on volume, long-term partnership potential, and payment terms. Request quotes from multiple suppliers to compare prices and services.
10. What are the typical lead times?
Lead times can vary from 30 to 60 days, depending on the order size and customization requirements. Always factor in shipping time when planning your order.
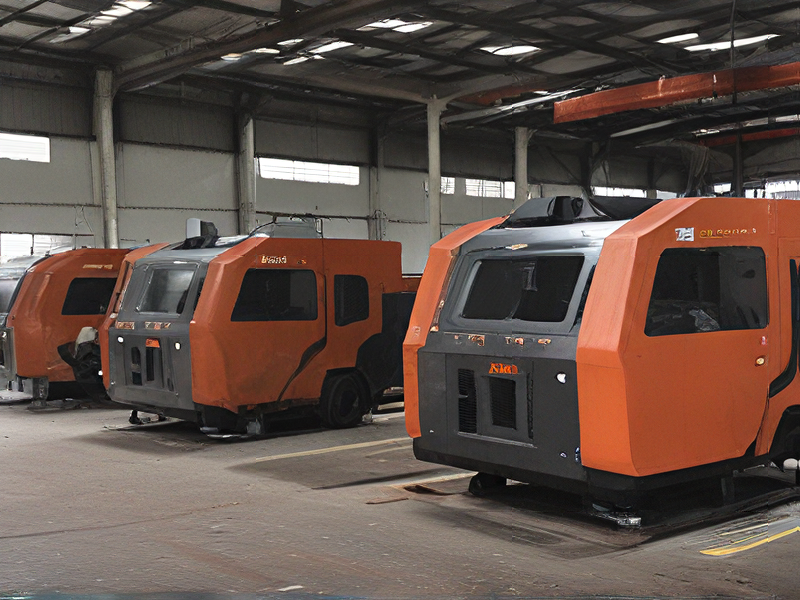