Technology and Applications of sheet metal parts
Sheet metal parts are integral components in various industries due to their versatility, durability, and cost-effectiveness. They are commonly used in automotive manufacturing, aerospace, electronics, construction, and consumer goods.
Technology: Sheet metal parts are typically fabricated through a process called sheet metal forming. This involves cutting, bending, and assembling thin metal sheets to create complex shapes and structures. Common techniques include:
1. Cutting: Laser cutting, water jet cutting, and plasma cutting are used to precisely cut sheet metal into desired shapes.
2. Bending: Press brakes or other forming equipment are used to bend the sheet metal to the required angles and configurations.
3. Joining: Welding, riveting, and adhesives are employed to assemble multiple sheet metal parts into larger assemblies.
Applications: Sheet metal parts find extensive use in:
1. Automotive Industry: Body panels, chassis components, and exhaust systems are made from sheet metal due to its strength and formability.
2. Aerospace: Structural components, such as fuselage panels and wing parts, require lightweight yet durable materials like aluminum and titanium sheet metal.
3. Electronics: Enclosures for electronic devices, such as computers and mobile phones, are often made from sheet metal for shielding and structural integrity.
4. Construction: Roofing, siding, and structural supports in buildings often utilize sheet metal due to its weather resistance and strength.
5. Consumer Goods: Household appliances, furniture, and kitchenware often incorporate sheet metal parts for both functional and aesthetic purposes.
Advancements in manufacturing technologies, such as computer-aided design (CAD) and computer numerical control (CNC) machining, have significantly enhanced the precision and efficiency of producing sheet metal parts. These technologies enable rapid prototyping and customization, making sheet metal an indispensable material in modern manufacturing across diverse industries.
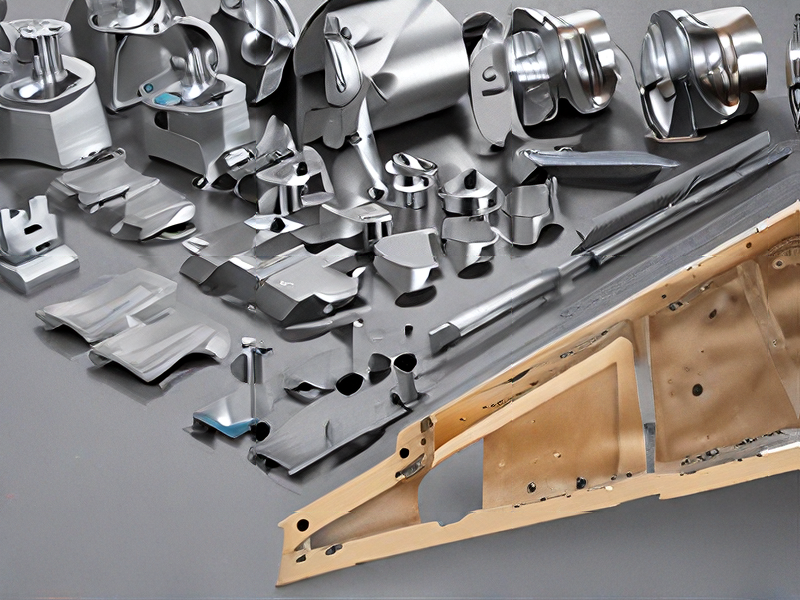
Quality Testing Methods for sheet metal parts and how to control quality
Quality testing methods for sheet metal parts typically include dimensional inspection, visual inspection, surface roughness measurement, hardness testing, and sometimes material composition analysis.
1. Dimensional Inspection: Use precision tools like calipers, micrometers, and CMM (Coordinate Measuring Machines) to ensure parts meet specified tolerances.
2. Visual Inspection: Check for defects like scratches, dents, burrs, and surface finish irregularities using visual aids like magnifiers and light sources.
3. Surface Roughness Measurement: Assess the texture and smoothness of surfaces using profilometers or surface roughness testers.
4. Hardness Testing: Verify material hardness to ensure it meets required specifications using methods like Rockwell or Vickers hardness testing.
5. Material Composition Analysis: Utilize techniques such as spectroscopy (e.g., X-ray fluorescence) to confirm material composition and ensure it aligns with standards.
To control quality, implement these practices:
1. Quality Management System (QMS): Establish clear procedures for inspection, testing, and documentation throughout production.
2. Training and Certification: Ensure personnel are trained in testing methods and equipment operation.
3. Statistical Process Control (SPC): Monitor production processes using SPC tools to detect and address variations before they affect product quality.
4. Supplier Quality Assurance: Set standards for suppliers and conduct audits to ensure incoming materials meet specifications.
5. Continuous Improvement: Use feedback from testing to identify areas for improvement and implement corrective actions.
By integrating these methods and controls, manufacturers can maintain consistent quality in sheet metal parts, meeting customer requirements and minimizing defects.
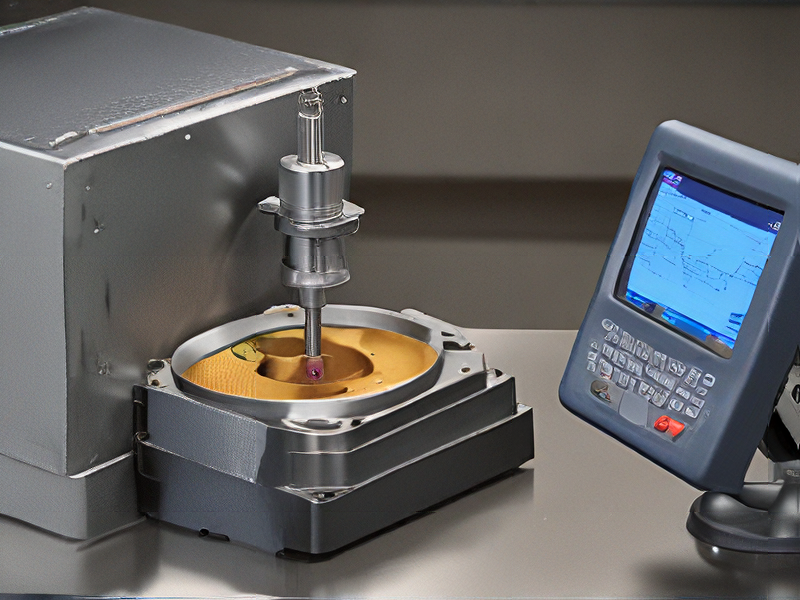
Tips for Procurement and Considerations when Purchasing from sheet metal parts
When procuring sheet metal parts, consider several key factors to ensure quality, cost-effectiveness, and timely delivery:
1. Material Selection: Choose the appropriate metal type (e.g., steel, aluminum) based on strength requirements, durability, and corrosion resistance needed for the application.
2. Supplier Capability: Assess the supplier’s experience and capability in manufacturing sheet metal parts. Look for certifications (ISO, AS9100) that ensure they meet industry standards.
3. Quality Assurance: Insist on quality control measures such as inspections, testing protocols, and adherence to specifications (e.g., tolerances, surface finish). Request samples or prototypes for validation.
4. Cost Considerations: Obtain detailed quotes that break down costs for materials, manufacturing processes, tooling, and any additional services (e.g., finishing, assembly). Consider total cost of ownership, including logistics and potential rework costs.
5. Lead Times and Flexibility: Evaluate the supplier’s ability to meet your production schedule. Discuss lead times, capacity, and flexibility in accommodating changes or rush orders.
6. Manufacturing Techniques: Understand the manufacturing techniques employed (e.g., laser cutting, stamping) and their impact on part quality, cost, and lead time. Ensure the supplier uses modern equipment and processes.
7. Supplier Communication: Establish clear communication channels for project updates, changes, and issue resolution. Ensure the supplier is responsive and proactive in addressing concerns.
8. Sustainability and Compliance: Verify the supplier’s commitment to environmental standards and regulations. Consider their approach to waste management, recycling, and ethical sourcing practices.
9. Long-Term Relationship: Aim for a partnership based on trust, reliability, and mutual benefit. Consider past performance and references from other clients.
By focusing on these considerations, you can streamline the procurement process for sheet metal parts, ensuring they meet your requirements for quality, cost, and delivery timelines.
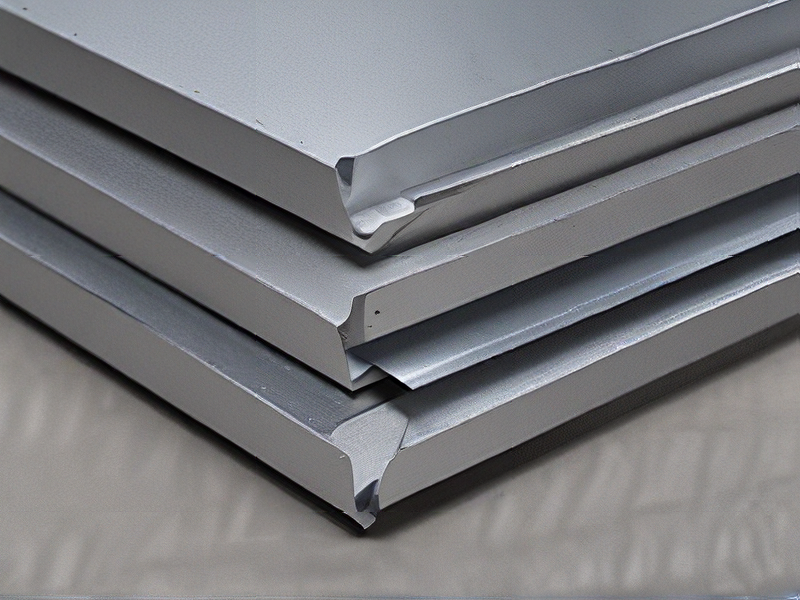
FAQs on Sourcing and Manufacturing from sheet metal parts in China
Certainly! When sourcing and manufacturing sheet metal parts in China, consider these FAQs:
1. How do I find reliable suppliers?
– Utilize online platforms like Alibaba or Made-in-China for initial searches. Verify suppliers through reviews, certifications, and direct communication.
2. What should I consider when choosing a supplier?
– Evaluate their experience with similar projects, production capacity, quality control measures, and responsiveness to inquiries.
3. How can I ensure product quality?
– Request samples for testing and inspection before bulk production. Implement clear quality standards and conduct factory visits or audits if feasible.
4. What are common challenges in manufacturing?
– Language barriers, cultural differences, intellectual property protection, and logistics management can pose challenges. Clear communication and legal agreements are crucial.
5. How do I manage logistics and shipping?
– Discuss shipping terms (FOB, CIF, etc.) and logistics arrangements upfront. Consider hiring a freight forwarder to simplify transportation and customs clearance.
6. What are the typical lead times?
– Lead times vary but generally range from weeks to months depending on complexity and order size. Clarify timelines early in the process.
7. How can I protect my intellectual property (IP)?
– Use non-disclosure agreements (NDAs) and ensure suppliers understand and respect your IP rights. Consider registering trademarks or patents where applicable.
8. What are the payment terms?
– Negotiate payment terms that balance supplier needs and your security. Consider using secure methods like letters of credit or trade finance for larger orders.
9. How do I handle quality control and inspections?
– Define quality control checkpoints throughout production. Consider hiring third-party inspectors or conducting inspections yourself before shipment.
10. What are the advantages of manufacturing in China?
– Cost-effectiveness, extensive manufacturing infrastructure, and flexibility in production capabilities make China a popular choice for sheet metal fabrication.
Navigating sourcing and manufacturing in China requires thorough research, clear communication, and careful management of logistics and quality control to ensure successful outcomes.
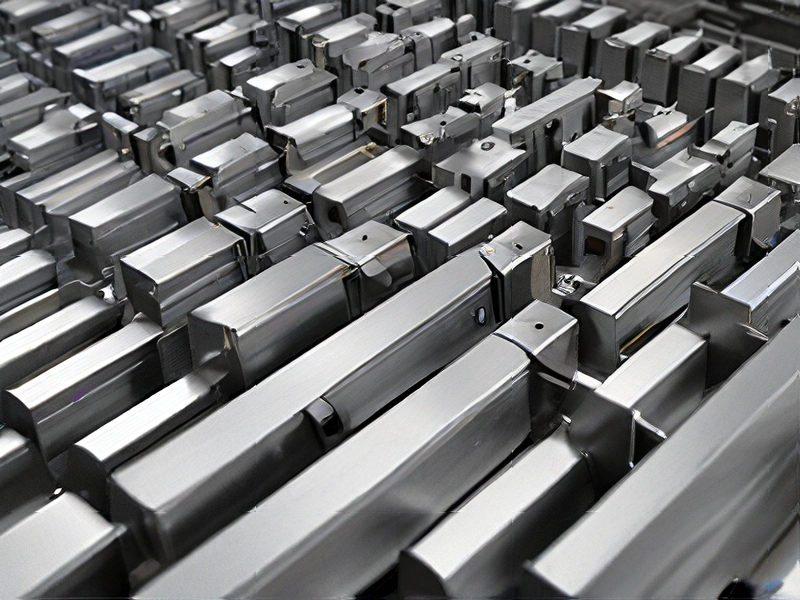