Technology and Applications of sheet metal shops
Sheet metal shops are specialized facilities that transform flat sheets of metal into various complex shapes and products using a variety of tools and techniques. The primary technologies and applications in these shops include:
Technologies
1. Cutting:
– Laser Cutting: Utilizes focused laser beams for precise cuts.
– Plasma Cutting: Employs a high-velocity jet of ionized gas for cutting thicker materials.
– Water Jet Cutting: Uses high-pressure water mixed with abrasives for cutting without heat distortion.
– Shearing: Involves cutting metal sheets with a blade.
2. Forming:
– Bending: Achieved using press brakes to bend metal sheets into specific angles.
– Stamping: Uses a press and dies to form or cut metal sheets into desired shapes.
– Roll Forming: Involves passing metal through rollers to achieve desired cross-sections.
3. Joining:
– Welding: Various methods like MIG, TIG, and spot welding are used to join metal pieces.
– Riveting: Mechanically fastening metal parts using rivets.
– Adhesive Bonding: Uses industrial adhesives for joining metals.
4. Finishing:
– Painting and Coating: Adds protective and aesthetic layers to the metal surfaces.
– Anodizing: Electrochemical process that increases corrosion resistance and wear.
Applications
1. Automotive: Sheet metal is essential for manufacturing car bodies, chassis, and other components.
2. Aerospace: Used in the production of aircraft skins, wings, and fuselage components.
3. Construction: Employed in building facades, roofing, and structural elements.
4. Electronics: Utilized for enclosures, brackets, and chassis for electronic devices.
5. Furniture: Creation of metal furniture, cabinetry, and fixtures.
6. HVAC: Manufacturing ducts, vents, and enclosures for heating, ventilation, and air conditioning systems.
Sheet metal shops leverage advanced technologies to produce high-precision, durable components for various industries, ensuring efficiency and innovation in manufacturing processes.
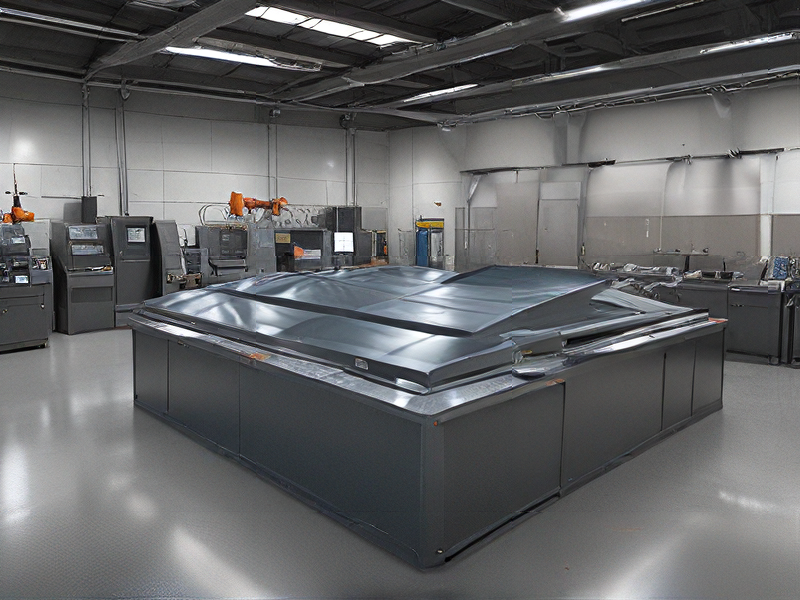
Quality Testing Methods for sheet metal shops and how to control quality
Quality testing methods for sheet metal shops typically involve a combination of visual inspection, dimensional measurement, and material testing. Visual inspection ensures surface defects like scratches, dents, or irregularities are detected. Dimensional measurement ensures parts conform to specified tolerances using tools such as calipers, micrometers, or coordinate measuring machines (CMMs). Material testing involves verifying the composition and mechanical properties through methods like hardness testing, tensile testing, or spectroscopy.
To control quality effectively, sheet metal shops implement several strategies:
1. Quality Management Systems (QMS): Establishing and maintaining QMS such as ISO 9001 ensures standardized processes and continuous improvement.
2. Training and Certification: Regular training for employees on inspection techniques and equipment operation ensures consistency in quality checks.
3. Statistical Process Control (SPC): Using SPC techniques monitors production processes, identifies trends, and prevents defects before they occur.
4. Supplier Quality Management: Ensuring raw materials meet specifications through rigorous supplier evaluation and audits.
5. Corrective and Preventive Actions (CAPA): Implementing CAPA processes addresses non-conformities promptly and prevents recurrence.
6. Documentation and Traceability: Maintaining comprehensive records allows tracing of materials and processes, aiding in identifying and rectifying quality issues.
By integrating these methods and controls, sheet metal shops can uphold high-quality standards, meet customer expectations, and improve overall operational efficiency.
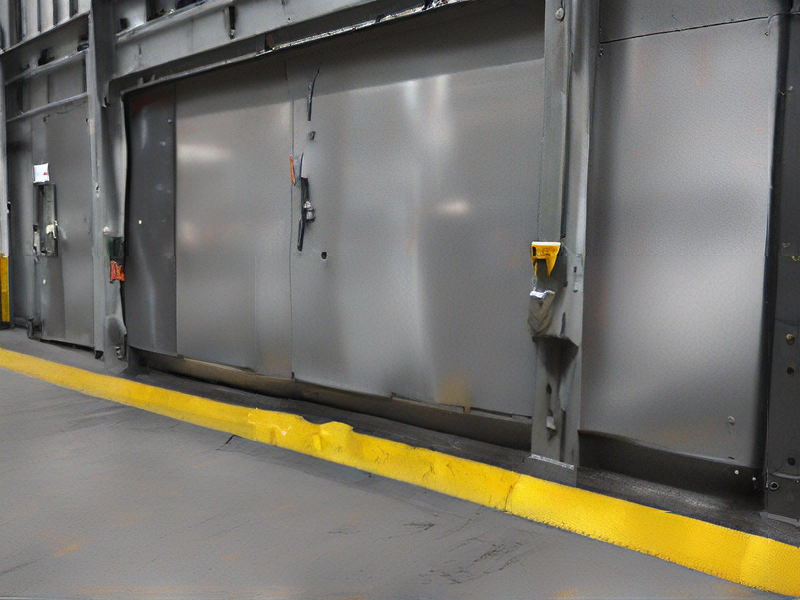
Tips for Procurement and Considerations when Purchasing from sheet metal shops
Tips for Procurement from Sheet Metal Shops
1. Define Requirements Clearly:
– Specify material type, thickness, tolerances, finishes, and any additional treatments.
– Provide detailed drawings and specifications to avoid misunderstandings.
2. Assess Vendor Capabilities:
– Ensure the shop has the necessary equipment and expertise for your project.
– Check for certifications and quality standards like ISO 9001.
3. Request Samples or Prototypes:
– Before placing a large order, request samples or prototypes to verify quality and precision.
– Use these samples to refine your specifications if needed.
4. Evaluate Lead Times:
– Confirm the shop’s production schedule and lead times.
– Ensure their timelines align with your project deadlines.
5. Cost Considerations:
– Obtain detailed quotes, including material costs, labor, tooling, and any additional charges.
– Compare quotes from multiple vendors to ensure competitive pricing.
6. Quality Assurance:
– Verify the shop’s quality control processes.
– Discuss inspection and testing methods to ensure parts meet your standards.
7. Communication and Support:
– Maintain open lines of communication for updates and troubleshooting.
– Establish a single point of contact to streamline interactions.
Considerations when Purchasing from Sheet Metal Shops
1. Material Selection:
– Choose the right material for your application, considering factors like strength, corrosion resistance, and weight.
2. Volume and Scalability:
– Assess the shop’s ability to handle your order volume, both current and future.
– Ensure they can scale production as needed.
3. Location and Logistics:
– Consider the shop’s location relative to your operations.
– Evaluate shipping costs and delivery times.
4. Vendor Reliability:
– Check the vendor’s track record for on-time delivery and consistency.
– Look for reviews or testimonials from other clients.
5. Compliance and Certifications:
– Ensure the shop complies with industry standards and regulations.
– Confirm certifications relevant to your industry, such as ISO or other quality management systems.
6. Technology and Innovation:
– Prefer shops that invest in advanced machinery and technology.
– Innovative processes like laser cutting or CNC machining can improve efficiency and quality.
By following these tips and considerations, you can ensure a successful procurement process and high-quality results from sheet metal shops.
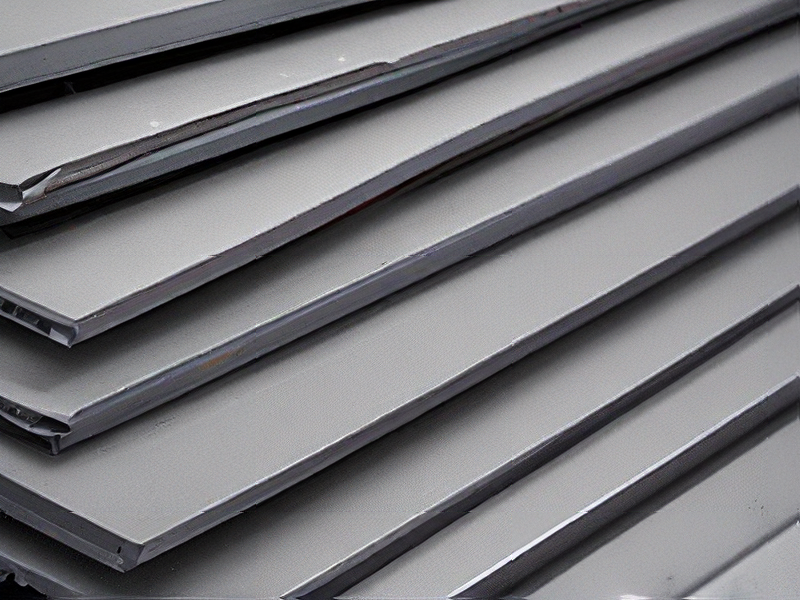
FAQs on Sourcing and Manufacturing from sheet metal shops in China
FAQs on Sourcing and Manufacturing from Sheet Metal Shops in China
1. Why source sheet metal parts from China?
– Cost-Effectiveness: Chinese manufacturers offer competitive pricing due to lower labor costs and economies of scale.
– Advanced Capabilities: Many Chinese factories are equipped with advanced machinery and technology for precise and high-quality production.
– Fast Turnaround: Efficient production processes often lead to shorter lead times.
2. How do I find reliable sheet metal manufacturers in China?
– Online Platforms: Use websites like Alibaba, Made-in-China, and Global Sources to find suppliers.
– Trade Shows: Attend trade fairs such as the Canton Fair to meet suppliers in person.
– Referrals and Networks: Utilize industry contacts and business networks for recommendations.
3. What should I consider when selecting a supplier?
– Experience and Expertise: Ensure the supplier has a proven track record in sheet metal fabrication.
– Certifications: Look for ISO and other relevant certifications.
– Quality Control: Verify the supplier’s quality control processes and request samples.
4. What is the typical production process for sheet metal parts?
– Design: Provide detailed CAD drawings and specifications.
– Prototyping: Initial prototypes are created to test and refine the design.
– Production: Once the prototype is approved, mass production begins.
– Quality Inspection: Regular inspections ensure compliance with standards.
5. How do I manage logistics and shipping?
– Incoterms: Understand terms like FOB, CIF, and DDP to determine responsibilities and costs.
– Freight Forwarders: Use experienced freight forwarders to handle shipping logistics.
– Customs Clearance: Ensure all necessary documentation is prepared for smooth customs clearance.
6. What are common challenges and how can I mitigate them?
– Communication Barriers: Use clear, concise communication and consider hiring a local agent.
– Quality Issues: Implement stringent quality checks and consider third-party inspections.
– Intellectual Property Risks: Use non-disclosure agreements (NDAs) and register patents if necessary.
7. How do I ensure long-term success with a Chinese supplier?
– Build Relationships: Foster strong relationships through regular visits and consistent communication.
– Continuous Improvement: Encourage ongoing improvements and provide feedback to maintain quality and efficiency.
By addressing these key points, you can navigate the complexities of sourcing and manufacturing from sheet metal shops in China effectively.
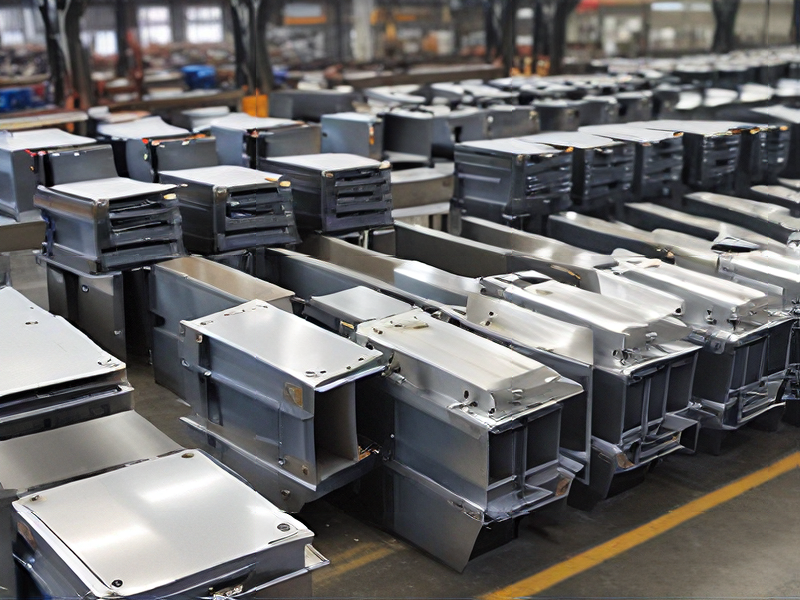