Technology and Applications of soft metals
Soft metals, such as lead, tin, and zinc, exhibit low melting points and are easily shaped or molded, making them valuable in various applications. Lead, due to its density and malleability, finds use in radiation shielding, batteries (lead-acid), and soldering. Its ability to absorb vibrations makes it suitable for soundproofing and construction materials. Tin, known for its corrosion resistance, is extensively used in electroplating to protect other metals. It also forms alloys like bronze (with copper) and pewter (with antimony), favored for decorative objects and statuettes.
Zinc, another soft metal, is crucial in galvanizing steel to prevent rusting, widely applied in construction for roofing and protective coatings. Alloys such as brass (copper-zinc) and solder (tin-zinc) are pivotal in electronics and plumbing for their conductivity and durability. Bismuth, notable for its low toxicity compared to lead, substitutes in applications like ammunition, fishing gear, and pharmaceuticals. Its low melting point supports its use in metal casting and as an alloy additive for tuning properties.
Soft metals’ properties cater to specialized applications in diverse industries, from manufacturing and construction to healthcare and electronics. Their adaptability in alloy formations enhances mechanical properties while maintaining their inherent characteristics, supporting a range of technological advancements and sustainable solutions across various sectors.
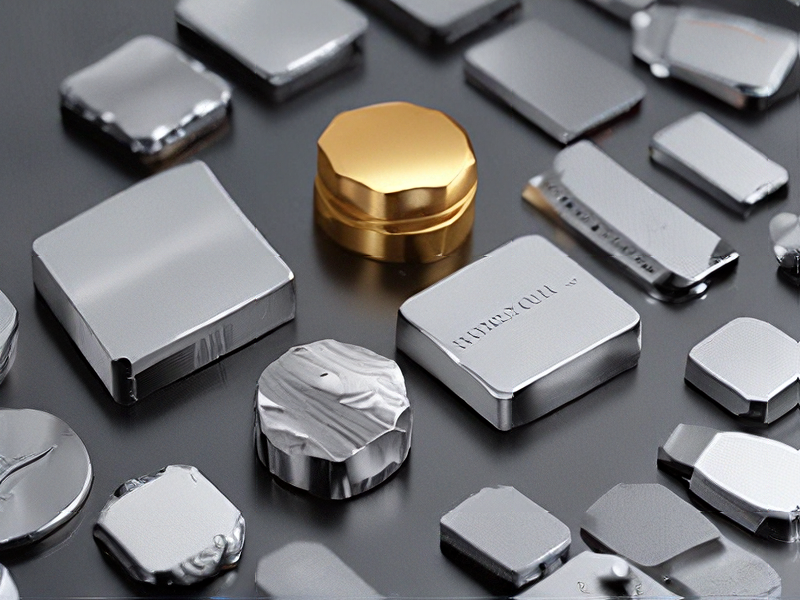
Quality Testing Methods for soft metals and how to control quality
Quality testing of soft metals involves various methods to ensure material properties and performance meet required standards. Key techniques include:
1. Tensile Testing: Measures the metal’s strength and ductility. A sample is pulled until it breaks, providing data on tensile strength, yield strength, and elongation.
2. Hardness Testing: Determines resistance to deformation. Common methods include Brinell, Rockwell, and Vickers hardness tests, where an indenter is pressed into the metal surface and the size or depth of the indentation is measured.
3. Chemical Analysis: Verifies the composition of the metal. Techniques like X-ray fluorescence (XRF) or spectroscopy ensure the alloy contains the correct elements in the proper proportions.
4. Microstructural Analysis: Examines the grain structure and phase distribution using optical microscopy or scanning electron microscopy (SEM). This helps identify defects and inconsistencies in the metal.
5. Impact Testing: Assesses the metal’s toughness, particularly at different temperatures. Charpy or Izod impact tests measure the energy absorbed by the metal when it fractures.
6. Non-Destructive Testing (NDT): Methods like ultrasonic testing, radiography, and dye penetrant testing detect internal and surface defects without damaging the metal. NDT is crucial for assessing the integrity of components in service.
Quality Control
1. Raw Material Inspection: Checking the quality of incoming materials through certificates of analysis and spot tests to ensure they meet specifications.
2. Process Control: Monitoring and controlling the manufacturing process parameters, such as temperature, pressure, and machining conditions, to maintain consistency.
3. In-Process Testing: Conducting periodic tests during production to catch defects early. This includes hardness checks and dimensional inspections.
4. Final Inspection: Comprehensive testing of the finished product to ensure it meets all specifications. This may involve a combination of the aforementioned tests.
5. Statistical Process Control (SPC): Using statistical methods to monitor and control production quality. This helps in identifying trends, variations, and potential issues before they become significant problems.
By integrating these methods, manufacturers can ensure the quality and reliability of soft metals in various applications.
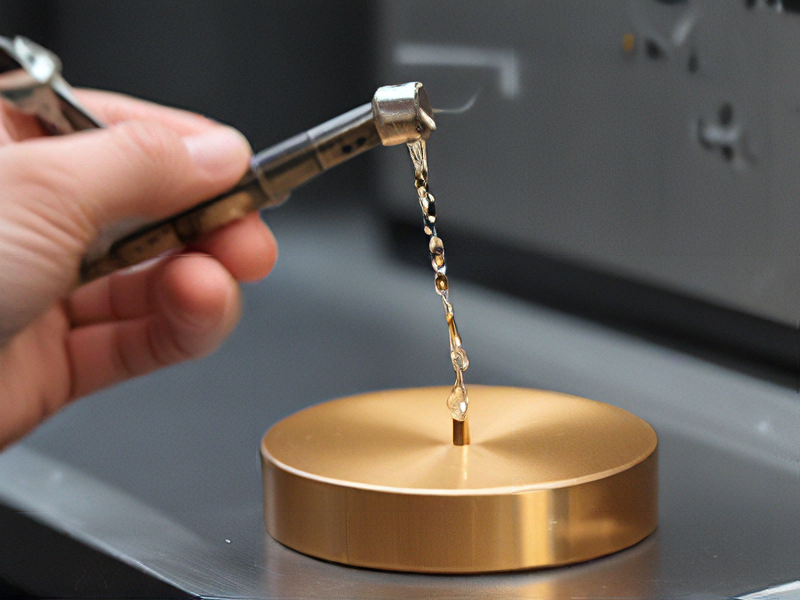
Tips for Procurement and Considerations when Purchasing from soft metals
When procuring soft metals, such as aluminum, copper, or lead, several key considerations can ensure you make informed purchasing decisions:
1. Material Specifications: Clearly define the required material specifications including alloy type, purity, grade, and physical dimensions. This ensures compatibility with your manufacturing or application requirements.
2. Supplier Selection: Choose reputable suppliers with a proven track record in delivering high-quality soft metals. Consider factors like reliability, certifications (ISO, quality standards), and their ability to meet your quantity and delivery timeline.
3. Price and Cost Factors: Evaluate quotations not only based on initial cost but also considering long-term costs such as maintenance, durability, and potential for recycling or reuse.
4. Quality Assurance: Request samples or certifications to verify material quality. Ensure compliance with industry standards to avoid material defects or performance issues.
5. Environmental Impact: Assess the environmental impact of sourcing soft metals. Opt for suppliers committed to sustainable practices and those offering recycled materials if applicable.
6. Supply Chain Resilience: Understand the supplier’s supply chain resilience, especially regarding potential disruptions or fluctuations in metal prices.
7. Logistics and Delivery: Plan logistics carefully to minimize transportation costs and risks associated with handling soft metals. Ensure packaging and handling meet safety standards to prevent damage during transit.
8. Legal and Compliance: Ensure compliance with local and international regulations concerning the procurement and use of soft metals, especially regarding hazardous materials or restricted substances.
9. Technical Support: Choose suppliers capable of providing technical support and expertise, particularly if custom alloys or specialized materials are required.
10. Feedback and Evaluation: Regularly review supplier performance and gather feedback from your production or operational teams to continuously improve procurement processes.
By integrating these considerations into your procurement strategy, you can effectively source soft metals that meet your quality, cost, and sustainability objectives while minimizing risks and ensuring operational efficiency.
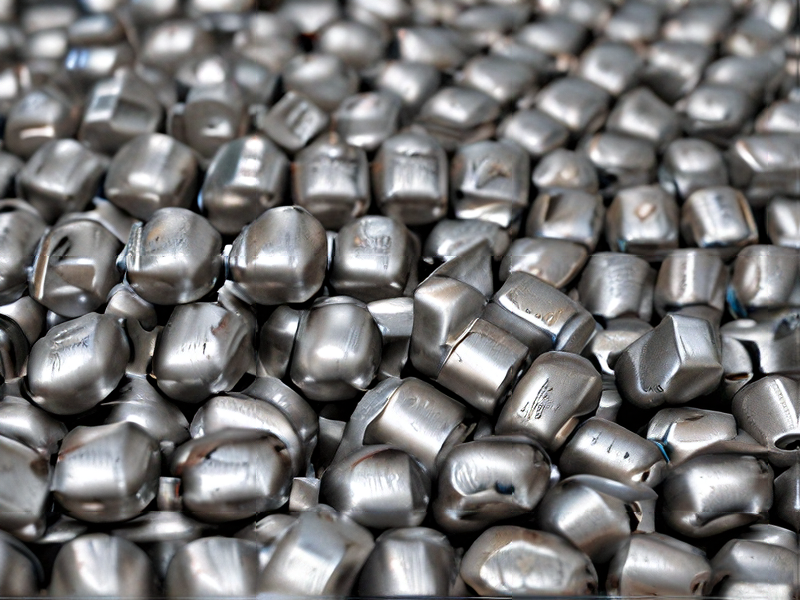
FAQs on Sourcing and Manufacturing from soft metals in China
FAQs on Sourcing and Manufacturing from Soft Metals in China
1. What are soft metals?
Soft metals are metals that are relatively easy to shape and mold, such as aluminum, lead, tin, zinc, and certain alloys. These materials are often used in industries like automotive, electronics, and construction.
2. Why source soft metals from China?
China offers competitive pricing, a large number of suppliers, advanced manufacturing capabilities, and a well-established supply chain for soft metals. This makes it a popular choice for businesses looking to reduce costs and enhance production efficiency.
3. How to find reliable suppliers in China?
Utilize online platforms like Alibaba, Global Sources, and Made-in-China. Additionally, attending trade fairs such as the Canton Fair can help identify and meet potential suppliers. Due diligence, including verifying certifications and factory visits, is crucial.
4. What certifications should I look for in a supplier?
Look for ISO certifications, particularly ISO 9001 for quality management. Other certifications like RoHS (Restriction of Hazardous Substances) and REACH (Registration, Evaluation, Authorization, and Restriction of Chemicals) can also be important depending on your industry.
5. What are common challenges in sourcing from China?
Common challenges include language barriers, cultural differences, quality control issues, and longer lead times. Engaging with local agents or sourcing companies can help mitigate these challenges.
6. How to ensure quality control?
Implement a rigorous quality control process that includes setting clear product specifications, conducting factory audits, and performing pre-shipment inspections. Hiring third-party inspection services can also be beneficial.
7. What are the shipping options for soft metals from China?
Shipping options include air freight, sea freight, and rail transport. Sea freight is often the most cost-effective for large volumes, while air freight is faster but more expensive. Rail transport is a viable option for shipments to Europe.
8. How do tariffs and trade policies affect sourcing from China?
Tariffs and trade policies can impact costs and logistics. Stay informed about current tariffs, anti-dumping duties, and trade agreements to avoid unexpected expenses.
9. What are the environmental regulations for soft metal manufacturing in China?
China has stringent environmental regulations that manufacturers must adhere to, including emissions controls and waste management. Ensuring your supplier complies with these regulations is crucial for sustainable and legal operations.
10. How to handle intellectual property (IP) concerns?
Protect your IP by registering it in China, using non-disclosure agreements (NDAs), and choosing suppliers with a good track record of respecting IP rights. Working with legal professionals familiar with Chinese IP law is advisable.
By addressing these FAQs, businesses can navigate the complexities of sourcing and manufacturing soft metals from China more effectively.
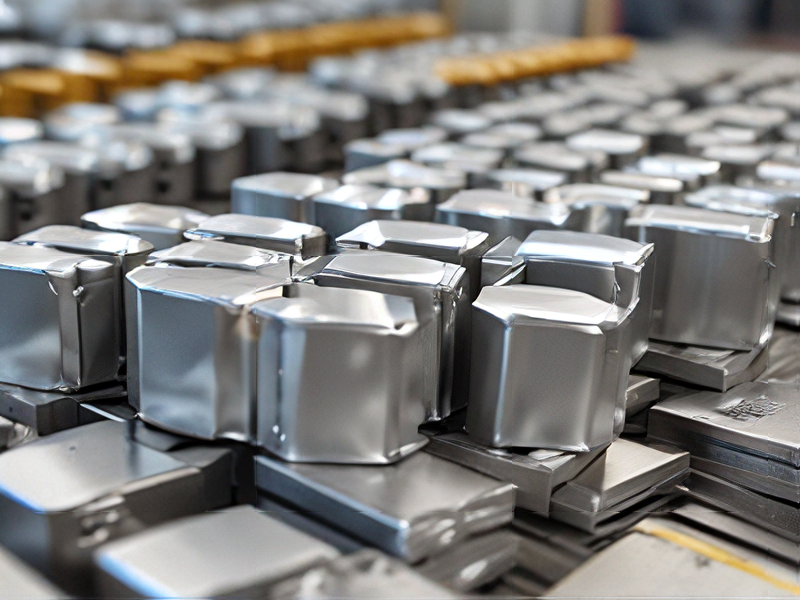