Technology and Applications of stainless steel 316s
Stainless steel 316S, an austenitic alloy, is renowned for its superior corrosion resistance, especially in chloride environments, making it ideal for various applications. Composed primarily of iron, chromium (16-18%), nickel (10-14%), and molybdenum (2-3%), this alloy exhibits enhanced strength and durability.
Technology:
The manufacturing process of 316S stainless steel involves several key technologies:
1. Melting and Casting: Initially, raw materials are melted in an electric arc furnace, followed by refining to achieve the desired composition. The molten steel is then cast into slabs.
2. Hot and Cold Working: The slabs are hot-rolled into sheets or plates, followed by cold working for enhanced strength and surface finish.
3. Heat Treatment: Annealing processes relieve internal stresses and improve ductility and corrosion resistance.
4. Surface Finishing: Techniques like pickling, passivation, and electropolishing enhance the surface quality and corrosion resistance.
Applications:
316S stainless steel is used across various industries due to its exceptional properties:
1. Marine Industry: Its resistance to saltwater corrosion makes it ideal for boat fittings, seawater systems, and coastal structures.
2. Chemical Processing: Used in tanks, valves, and piping for handling corrosive substances.
3. Medical Devices: Employed in surgical instruments, implants, and orthopedic devices due to its biocompatibility and sterilization capability.
4. Food and Beverage: Used in equipment like storage tanks, food processing machinery, and kitchen appliances because it does not affect food flavor and is easy to clean.
5. Construction: Utilized in architectural facades, handrails, and structural components for its aesthetic appeal and durability.
6. Oil and Gas: Employed in pipelines, heat exchangers, and offshore platforms for its robustness in harsh environments.
In summary, stainless steel 316S stands out due to its combination of mechanical strength, excellent corrosion resistance, and versatility, making it a preferred material in demanding applications across multiple industries.
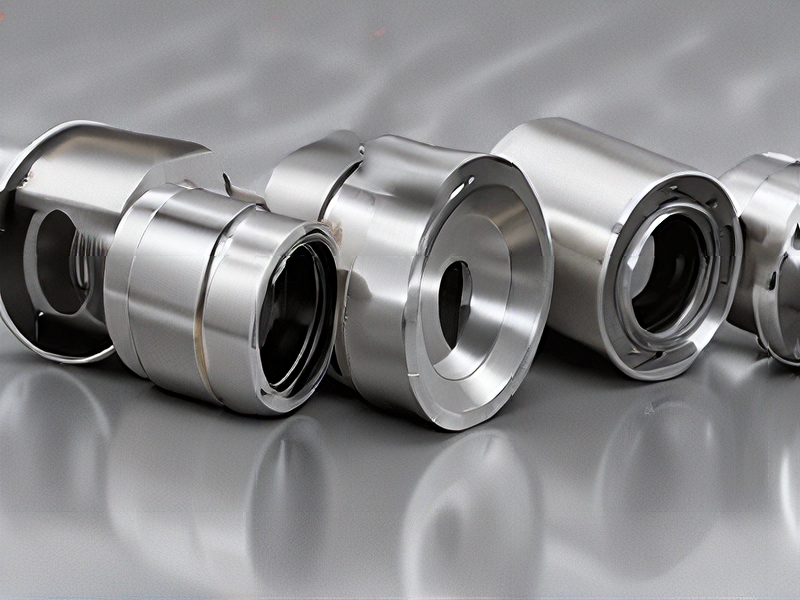
Quality Testing Methods for stainless steel 316s and how to control quality
Quality Testing Methods for Stainless Steel 316:
1. Chemical Analysis:
– Spectroscopy: Determines the elemental composition, ensuring it meets the required standards for stainless steel 316 (e.g., chromium, nickel, molybdenum content).
– Wet Chemical Analysis: Traditional method to confirm alloy composition.
2. Mechanical Testing:
– Tensile Test: Measures the material’s strength and ductility.
– Hardness Test: Determines resistance to deformation using Rockwell, Brinell, or Vickers methods.
– Impact Test: Assesses toughness, typically using the Charpy V-notch method.
3. Non-Destructive Testing (NDT):
– Ultrasonic Testing (UT): Detects internal flaws or inclusions.
– Radiographic Testing (RT): Uses X-rays or gamma rays to visualize internal defects.
– Magnetic Particle Testing (MPT): Identifies surface and near-surface discontinuities.
– Dye Penetrant Testing (DPT): Reveals surface-breaking defects.
4. Corrosion Testing:
– Pitting Resistance Test: Assesses resistance to pitting corrosion.
– Intergranular Corrosion Test: Ensures resistance to corrosion along grain boundaries.
– Salt Spray Test: Evaluates overall corrosion resistance in a simulated corrosive environment.
5. Microstructural Analysis:
– Optical Microscopy: Examines the grain structure and phase distribution.
– Scanning Electron Microscopy (SEM): Provides detailed images of the microstructure and can analyze elemental composition via EDS (Energy Dispersive X-ray Spectroscopy).
Quality Control Methods:
1. Raw Material Inspection:
– Verify supplier certifications.
– Conduct incoming material testing to ensure compliance with specifications.
2. Process Control:
– Monitor and control manufacturing processes.
– Implement Statistical Process Control (SPC) to track and minimize variations.
3. Final Product Inspection:
– Perform dimensional checks.
– Conduct final NDT and mechanical tests to ensure product integrity.
4. Documentation and Traceability:
– Maintain thorough records of all tests and inspections.
– Ensure each batch of stainless steel 316 can be traced back to its raw material lot and production parameters.
5. Continuous Improvement:
– Implement feedback loops from testing and customer feedback to improve processes and material quality continuously.
These methods ensure the reliability and performance of stainless steel 316 in various applications.
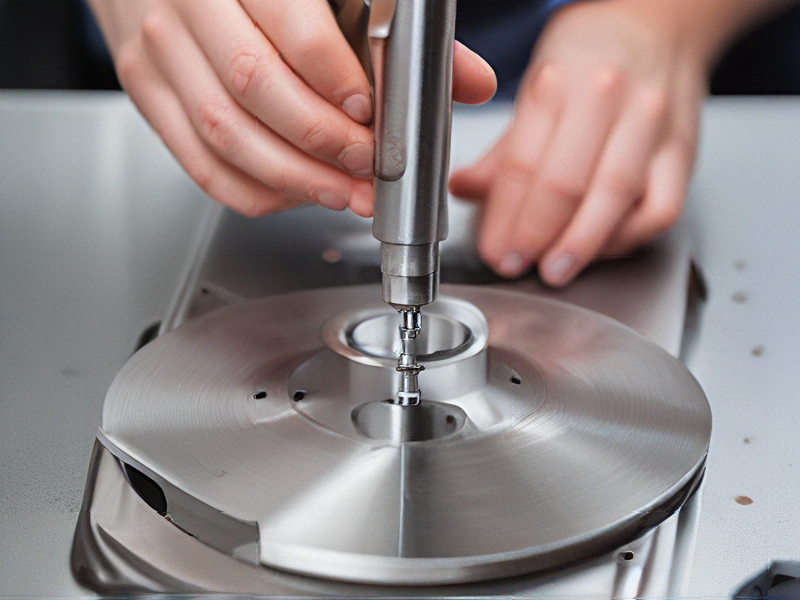
Tips for Procurement and Considerations when Purchasing from stainless steel 316s
When procuring stainless steel 316s, consider the following tips and factors to ensure you make the best purchasing decisions:
1. Understand Specifications: Stainless steel 316 is known for its corrosion resistance, strength, and durability. Ensure you understand its properties, including resistance to pitting and crevice corrosion, which is vital for marine and chloride environments.
2. Quality and Standards: Verify that the material meets relevant standards such as ASTM, ISO, or EN. Quality certificates and compliance documentation from suppliers are essential for confirming this.
3. Supplier Reliability: Choose suppliers with a strong reputation for quality and reliability. Check reviews, ask for references, and consider their experience in supplying stainless steel 316s.
4. Testing and Certification: Ensure the material has been tested and certified. Look for certifications like Mill Test Reports (MTRs) that detail the chemical composition and mechanical properties of the steel.
5. Cost Considerations: While price is a significant factor, it should not be the sole determinant. Balance cost with quality, reliability, and the specific requirements of your application.
6. Surface Finish and Form: Stainless steel 316s is available in various finishes (e.g., brushed, polished) and forms (e.g., sheets, bars, tubes). Choose the finish and form that best suits your application needs.
7. Sustainability and Compliance: Consider the environmental impact and ensure the supplier adheres to sustainability practices and regulatory requirements.
8. Technical Support: Opt for suppliers who offer strong technical support, including guidance on material selection, usage, and after-sales service.
9. Lead Time and Availability: Ensure that the supplier can meet your required lead times and has sufficient stock or production capacity to fulfill your order promptly.
10. Logistics and Packaging: Assess the supplier’s logistics capabilities and ensure proper packaging to avoid damage during transportation.
By considering these factors, you can ensure that your procurement process for stainless steel 316s is efficient, cost-effective, and meets the specific needs of your project.
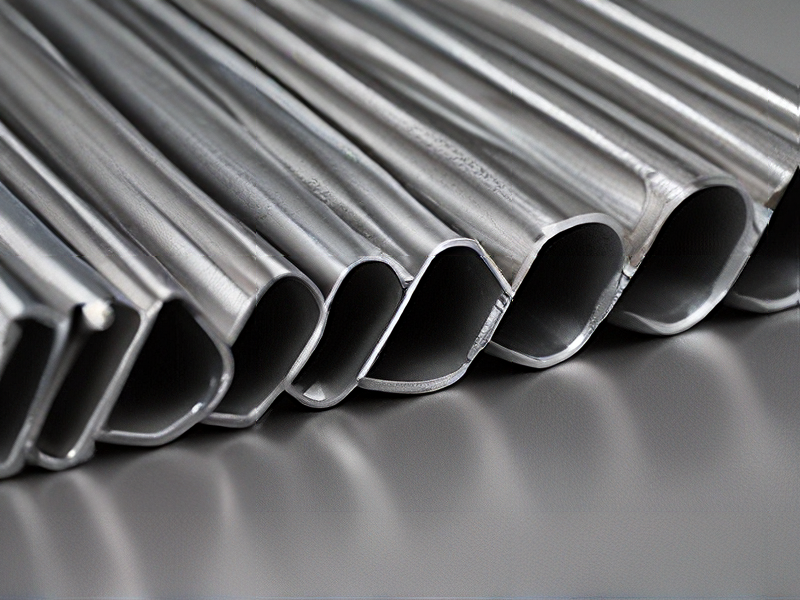
FAQs on Sourcing and Manufacturing from stainless steel 316s in China
FAQs on Sourcing and Manufacturing from Stainless Steel 316s in China
1. Why choose stainless steel 316s?
Stainless steel 316s is known for its superior corrosion resistance, especially in chloride environments, making it ideal for marine, chemical, and medical applications.
2. Why source stainless steel 316s from China?
China offers competitive pricing, a wide range of suppliers, and extensive manufacturing capabilities, ensuring cost efficiency and high-quality production.
3. How to find reliable suppliers?
Utilize platforms like Alibaba, Global Sources, and Made-in-China. Verify suppliers through reviews, certifications (ISO, SGS), and by requesting samples.
4. What certifications should suppliers have?
Look for ISO 9001 for quality management, ASTM standards for material specifications, and other relevant certifications based on your industry needs.
5. What are the key considerations when sourcing?
Evaluate supplier reputation, production capacity, quality control processes, and adherence to international standards. Also, consider communication efficiency and lead times.
6. What are the typical lead times?
Lead times can vary from 2 to 8 weeks depending on the complexity of the order and the supplier’s schedule. Custom products may take longer.
7. How to ensure product quality?
Implement rigorous quality checks, request detailed material test reports (MTRs), and consider third-party inspections. On-site visits can also be beneficial.
8. What are the common manufacturing processes?
Processes include casting, forging, machining, and welding. Each process depends on the product specifications and end-use requirements.
9. How to handle shipping and logistics?
Choose reliable freight forwarders, understand import regulations, and ensure proper packaging to prevent damage during transit. Incoterms (FOB, CIF) can define shipping responsibilities.
10. What are the potential risks?
Risks include quality issues, communication barriers, and longer lead times. Mitigate these by working with reputable suppliers and maintaining clear, documented agreements.
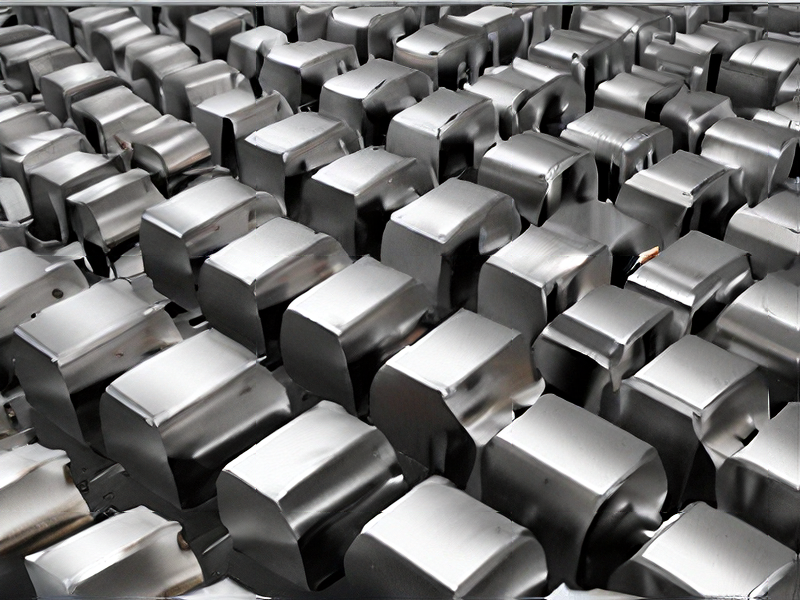