Technology and Applications of welding and sheet metal
Welding and sheet metal fabrication are crucial in manufacturing and construction industries. Welding joins materials like metals or thermoplastics by melting them together, often using heat and pressure. Common welding techniques include arc welding (using electric currents), gas welding (using combustible gases), and laser welding (using high-powered lasers). Applications range from automotive manufacturing to aerospace, where precision and durability are paramount.
Sheet metal fabrication involves forming thin metal sheets into desired shapes through cutting, bending, and assembling processes. Computer Numerical Control (CNC) machines enhance accuracy and efficiency in cutting and shaping sheet metals, used extensively in HVAC systems, electronics enclosures, and architectural components.
Advanced technologies like robotic welding systems and 3D metal printing (additive manufacturing) have revolutionized welding and sheet metal applications. Robotic welding ensures consistent weld quality and productivity, while 3D metal printing enables complex geometries and customization.
Challenges include ensuring weld integrity under varying conditions and minimizing material distortion during fabrication. Innovations continue to focus on automation, material efficiency, and sustainability, addressing demands for lighter, stronger, and environmentally friendly products.
Overall, welding and sheet metal technologies play crucial roles in modern manufacturing, supporting diverse industries with their versatile applications and evolving capabilities.
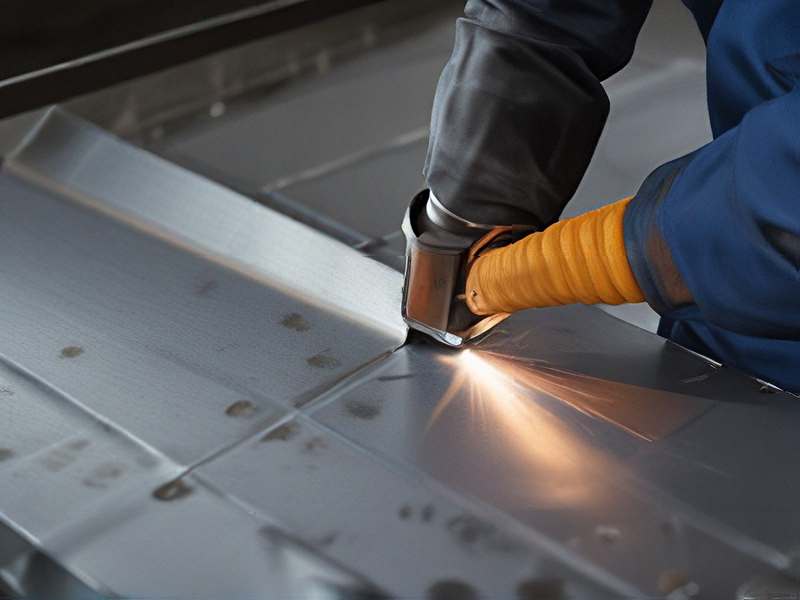
Quality Testing Methods for welding and sheet metal and how to control quality
Quality testing methods for welding and sheet metal typically include:
1. Visual Inspection: This involves examining the welded joints or sheet metal surfaces for defects such as cracks, porosity, incomplete fusion, or surface irregularities.
2. Destructive Testing: Techniques like tensile testing, bend testing, and impact testing are used to assess the mechanical properties and strength of welds or sheet metal.
3. Non-Destructive Testing (NDT): Methods such as ultrasonic testing (UT), radiographic testing (RT), magnetic particle testing (MT), and dye penetrant testing (PT) are employed to detect internal defects without damaging the material.
4. Dimensional Inspection: Ensures that welded assemblies or sheet metal components meet specified dimensional tolerances and geometrical requirements.
To control quality:
– Establish Standards: Define clear quality standards and acceptance criteria for welds and sheet metal components.
– Qualified Personnel: Ensure personnel performing welding and inspection are trained and certified according to relevant standards (e.g., AWS, ASME).
– Process Control: Monitor welding parameters (e.g., voltage, current, travel speed) and sheet metal forming processes to maintain consistency and quality.
– Documentation: Maintain comprehensive records of inspection results, welder qualifications, and process parameters for traceability and future reference.
– Continuous Improvement: Implement feedback mechanisms to address issues and improve processes continually.
By employing these methods and controls, manufacturers can consistently produce high-quality welded assemblies and sheet metal components that meet customer specifications and regulatory requirements.
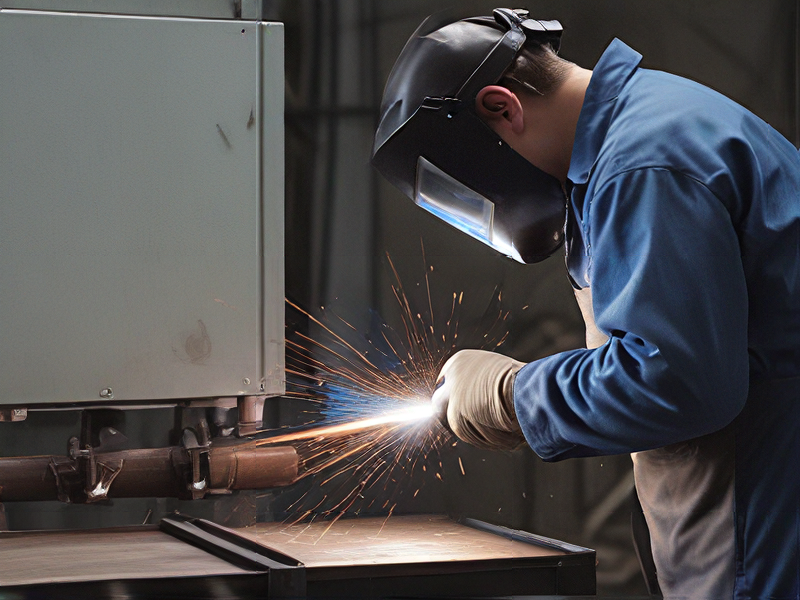
Tips for Procurement and Considerations when Purchasing from welding and sheet metal
When procuring welding and sheet metal services, several key considerations can streamline the purchasing process:
1. Supplier Qualification: Ensure suppliers are certified and have a proven track record in welding and sheet metal fabrication. Look for certifications such as AWS (American Welding Society) for welders and ISO 9001 for quality management systems.
2. Quality Standards: Specify your quality requirements clearly. Check if the supplier has quality assurance processes in place, such as inspections and testing protocols for welded joints and metal components.
3. Capabilities and Equipment: Evaluate the supplier’s capabilities and equipment. They should have the necessary machinery for cutting, bending, and welding various metals like steel, aluminum, and stainless steel.
4. Material Sourcing: Verify where the supplier sources their materials from. Ensure they use high-quality metals suitable for your project requirements.
5. Cost and Pricing: Obtain detailed pricing proposals that include material costs, labor, overheads, and any additional fees. Compare quotes from multiple suppliers to ensure competitiveness without compromising on quality.
6. Lead Times and Flexibility: Discuss lead times and their flexibility to accommodate your project timeline. Consider their ability to scale production if needed.
7. Communication and Support: Effective communication is crucial. Choose suppliers who are responsive and provide clear updates throughout the project lifecycle.
8. Past Performance and References: Request references or case studies from previous projects similar to yours. This can provide insights into their performance, reliability, and adherence to deadlines.
9. Contractual Agreements: Establish clear contractual agreements covering delivery schedules, payment terms, quality expectations, and dispute resolution mechanisms.
10. Sustainability Practices: Inquire about their sustainability initiatives and practices, such as recycling programs or energy-efficient processes, to align with your company’s environmental goals.
By focusing on these considerations, you can ensure a smoother procurement process and select a welding and sheet metal supplier that meets your project requirements effectively.
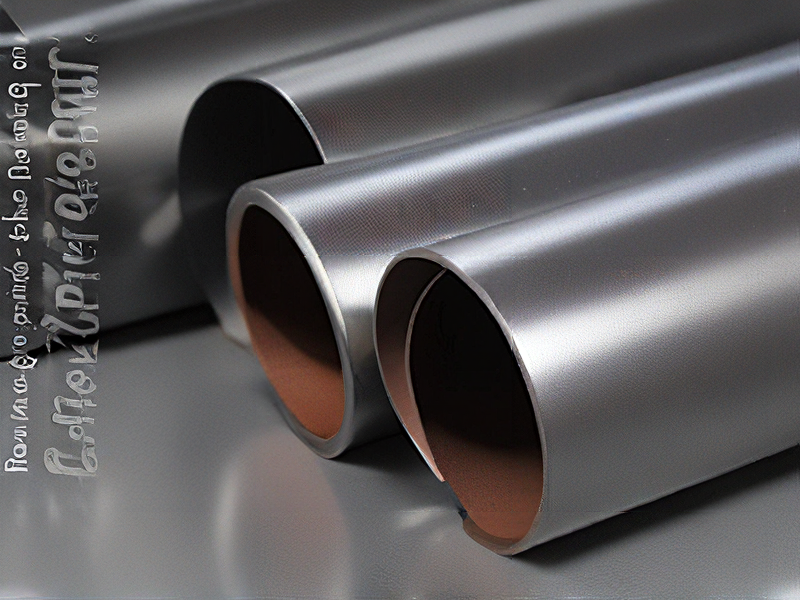
FAQs on Sourcing and Manufacturing from welding and sheet metal in China
FAQs on Sourcing and Manufacturing from Welding and Sheet Metal in China
1. Why should I consider sourcing welding and sheet metal from China?
China offers competitive pricing, a vast selection of suppliers, advanced manufacturing technologies, and extensive experience in welding and sheet metal fabrication. These factors contribute to cost savings and high-quality production.
2. How do I find reliable suppliers in China?
Utilize platforms like Alibaba, Made-in-China, and Global Sources to find suppliers. Additionally, attend trade shows such as the Canton Fair and consult sourcing agents or third-party verification services to ensure supplier credibility.
3. What are the common welding techniques used by Chinese manufacturers?
Chinese manufacturers commonly use MIG, TIG, and Arc welding techniques. These methods are chosen based on the material type, thickness, and the required precision of the weld.
4. What materials are typically available for sheet metal fabrication?
Materials commonly used include stainless steel, aluminum, carbon steel, and galvanized steel. These materials are available in various grades to meet different application requirements.
5. How do I ensure the quality of the products?
Conduct thorough supplier audits, request material certifications, and implement stringent quality control measures. Consider third-party inspections and sample testing before mass production.
6. What are the lead times for production and shipping?
Lead times vary depending on the complexity and quantity of the order. Typically, production takes 4-6 weeks, with additional shipping times ranging from 2-6 weeks depending on the shipping method.
7. What are the typical payment terms?
Common payment terms include a 30% deposit upfront and the remaining 70% upon shipment. Letter of Credit (LC) and Trade Assurance (through Alibaba) are also popular options to protect both parties.
8. Are there any risks involved?
Potential risks include communication barriers, quality inconsistencies, and intellectual property concerns. Mitigate these risks by maintaining clear communication, conducting regular inspections, and using Non-Disclosure Agreements (NDAs).
9. How can I handle logistics and customs clearance?
Work with experienced freight forwarders and customs brokers to manage logistics and ensure smooth customs clearance. Familiarize yourself with import regulations and tariffs in your country.
10. What are the benefits of long-term partnerships with Chinese suppliers?
Long-term partnerships can lead to better pricing, improved product quality, and more reliable delivery schedules. Building strong relationships also facilitates better communication and cooperation.
By considering these FAQs, you can navigate the complexities of sourcing and manufacturing welding and sheet metal products from China effectively.
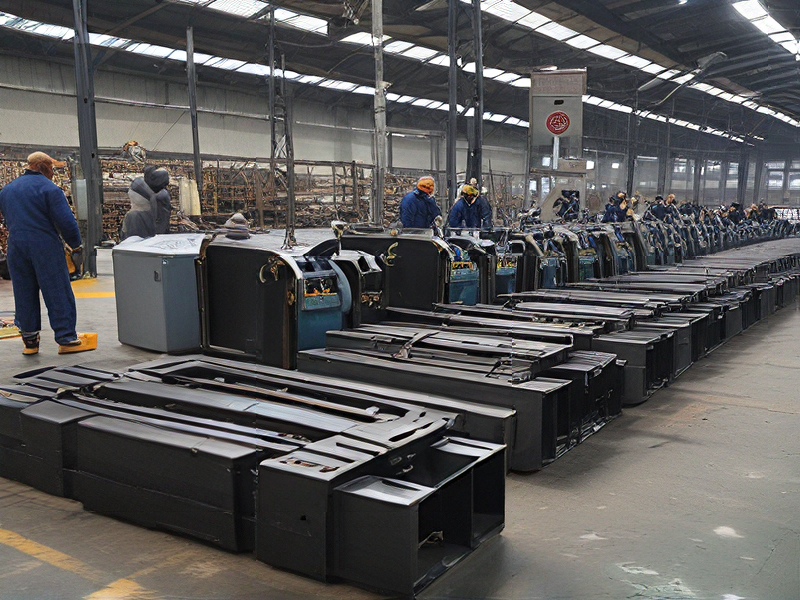