Technology and Applications of what is a miller machine
A Miller machine, also known as a Miller oscillator or Miller integrator, is an electronic circuit used primarily in analog applications for generating sinusoidal oscillations or for integrating signals. It consists of an operational amplifier (op-amp) configured with a feedback network that typically includes a capacitor and sometimes a resistor.
Technology:
The core technology revolves around the operational amplifier, which serves as the active component. Op-amps are chosen for their high gain, allowing the Miller machine to produce stable oscillations or accurately integrate input signals. The feedback network, typically a capacitor in parallel with a resistor, determines the frequency of oscillation or the integration characteristics.
Applications:
1. Oscillator: In oscillation mode, the Miller machine is used in signal generation, such as in audio oscillators, function generators, and in communication systems for generating carrier signals.
2. Integrator: As an integrator, it computes the integral of an input voltage signal over time. This functionality is crucial in analog computing, waveform shaping, and in applications requiring precise integration, such as in control systems and analog signal processing.
3. Waveform Generation: Beyond pure sinusoidal signals, Miller machines can generate various waveforms by adjusting the feedback network components, offering versatility in signal synthesis for testing and measurement purposes.
4. Filtering: In some configurations, Miller machines can function as low-pass or band-pass filters, contributing to their utility in analog signal conditioning and processing.
Overall, Miller machines leverage the operational amplifier’s characteristics and the feedback network’s configuration to serve diverse roles in analog electronics, spanning from basic signal generation to complex waveform synthesis and analog computation tasks.
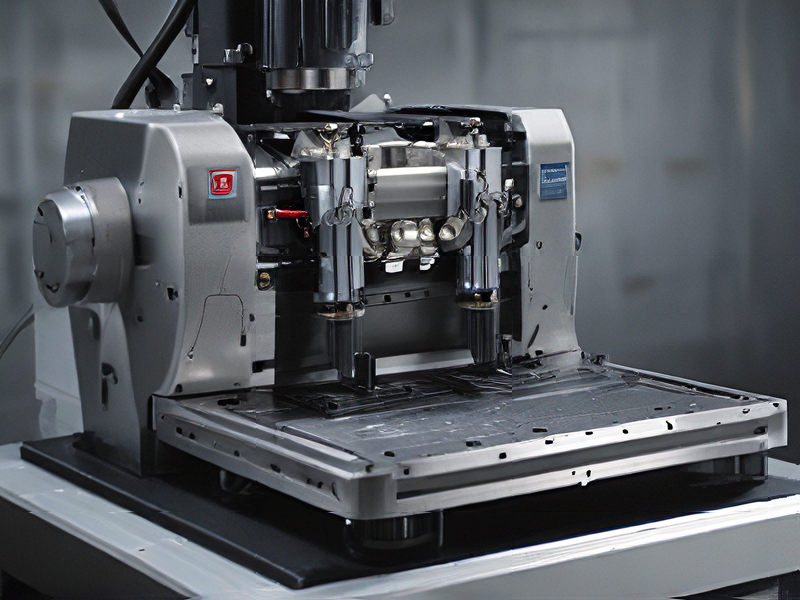
Quality Testing Methods for what is a miller machine and how to control quality
A milling machine is a tool used to shape solid materials, typically metals, into precise shapes and sizes through the use of rotary cutters. Quality control in milling machines is crucial to ensure the accuracy and reliability of the machined parts. Here are some effective methods:
1. Dimensional Inspection: Use precision measurement tools like calipers, micrometers, and coordinate measuring machines (CMMs) to verify the dimensions of machined parts against design specifications.
2. Surface Roughness Measurement: Evaluate the surface finish using instruments such as profilometers to ensure it meets required standards, which is crucial for parts where smoothness impacts performance.
3. Visual Inspection: Inspect parts visually for defects such as cracks, burrs, and surface irregularities. Proper lighting and magnification aids in detecting imperfections.
4. Tool Wear Monitoring: Regularly check cutting tools for wear and tear using tool pre-setters or wear monitoring systems. Replace worn tools promptly to maintain machining accuracy.
5. Process Control: Implement process parameters monitoring (e.g., spindle speed, feed rate, coolant flow) to ensure consistency and adherence to machining standards. Use sensors and monitoring software for real-time data collection.
6. Statistical Process Control (SPC): Utilize SPC techniques to monitor machining variations over time, identify trends, and take corrective actions to prevent defects.
7. Material Inspection: Verify the quality of raw materials before machining to prevent defects caused by material impurities or incorrect material properties.
8. Operator Training and Certification: Ensure operators are trained in machining techniques, equipment operation, and quality standards. Certification programs can validate their proficiency.
By integrating these methods, manufacturers can effectively control the quality of machined parts produced by milling machines, ensuring they meet specifications and customer expectations reliably.
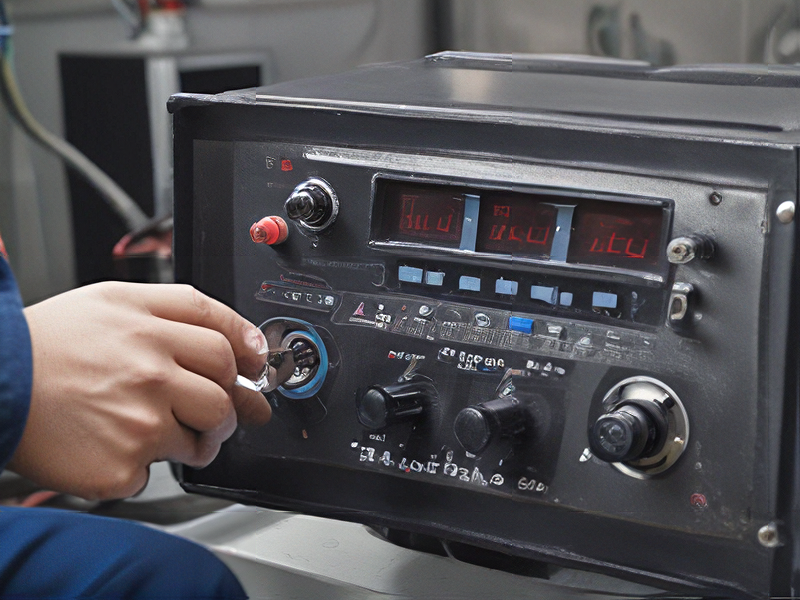
Tips for Procurement and Considerations when Purchasing from what is a miller machine
Tips for Procurement and Considerations when Purchasing a Milling Machine
#### 1. Understand Your Needs:
– Material Types: Determine the types of materials you’ll be working with (e.g., metal, wood, plastic) as this affects the machine’s specifications.
– Workload: Assess the volume and complexity of tasks to choose between light-duty or heavy-duty machines.
#### 2. Key Specifications:
– Spindle Speed and Motor Power: Ensure the machine has adjustable spindle speeds and sufficient motor power to handle various materials.
– Table Size and Travel: Verify the table size and travel distance in X, Y, and Z axes to accommodate your workpieces.
– Accuracy and Precision: Check the machine’s tolerance levels and repeatability to meet your precision requirements.
#### 3. Types of Milling Machines:
– Vertical vs. Horizontal: Vertical mills are versatile and user-friendly, while horizontal mills are suitable for heavy-duty tasks.
– CNC vs. Manual: CNC machines offer automation and precision but are more expensive. Manual machines are cost-effective but require skilled operators.
#### 4. Brand and Manufacturer Reputation:
– Research manufacturers for reliability, quality of machines, and after-sales support. Read reviews and ask for recommendations.
#### 5. Budget and Cost:
– Consider not just the initial purchase price but also the long-term costs, including maintenance, tooling, and potential upgrades.
#### 6. Support and Training:
– Ensure the manufacturer provides adequate training and technical support to maximize the machine’s utility.
#### 7. Safety Features:
– Check for essential safety features such as emergency stops, protective guards, and proper ventilation systems.
#### 8. Warranty and Service:
– Evaluate the warranty terms and the availability of service centers to ensure prompt repairs and maintenance.
By considering these factors, you can make a well-informed decision that aligns with your operational needs and budget, ensuring efficiency and precision in your milling tasks.
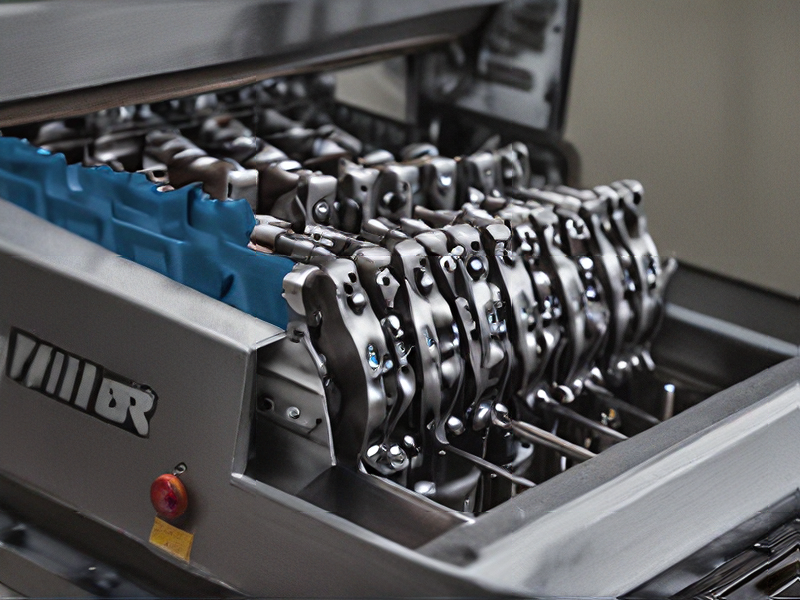
FAQs on Sourcing and Manufacturing from what is a miller machine in China
FAQs on Sourcing and Manufacturing in China
1. What is a miller machine in China?
A miller machine, commonly known as a milling machine, is a device used in manufacturing to remove material from a workpiece using rotary cutters. In China, these machines are widely used in various industries, including automotive, aerospace, and electronics, due to their precision and efficiency.
2. Why source from China?
China offers competitive pricing, a vast supplier base, and advanced manufacturing capabilities. Many Chinese manufacturers are capable of producing high-quality products at lower costs due to economies of scale and advanced technology.
3. How do I find reliable suppliers?
Use online platforms like Alibaba, Made-in-China, and Global Sources. Verify suppliers through site visits, third-party audits, and checking certifications such as ISO. Trade shows and sourcing fairs can also be valuable for direct contact.
4. What are the common challenges?
Language barriers, quality control issues, and intellectual property concerns are common challenges. Mitigate these by hiring local agents, conducting thorough quality inspections, and using contracts to protect IP.
5. How can I ensure product quality?
Implement stringent quality control processes, including pre-production samples, in-process inspections, and final quality checks. Consider using third-party inspection services.
6. What is the lead time for manufacturing?
Lead times vary based on product complexity and order volume but typically range from 30 to 60 days. Account for additional time for shipping and customs clearance.
7. What are the payment terms?
Common payment terms include T/T (Telegraphic Transfer), L/C (Letter of Credit), and trade assurance services offered by platforms like Alibaba. It’s advisable to negotiate payment terms that balance risk and trust.
8. How do I handle shipping and logistics?
Work with experienced freight forwarders who can handle customs documentation, shipping arrangements, and logistics management. Consider the mode of transport (air, sea, or rail) based on cost and urgency.
9. Are there any legal considerations?
Ensure compliance with local regulations, import/export laws, and product standards. Engage legal counsel familiar with international trade to draft contracts and handle disputes.
10. How can I protect my intellectual property (IP)?
Register your trademarks, patents, and designs in China. Use non-disclosure agreements (NDAs) and work with suppliers who have a reputation for respecting IP.
By addressing these FAQs, businesses can navigate the complexities of sourcing and manufacturing in China more effectively.
