Technology and Applications of wood cnc
Wood CNC (Computer Numerical Control) technology revolutionizes woodworking by automating processes with precision and flexibility. Utilizing CAD (Computer-Aided Design) software, wood CNC machines translate digital designs into precise cuts, carvings, and engravings on wood. This technology offers several applications across various industries and crafts.
In furniture manufacturing, CNC machines enable efficient production of complex designs, from intricate chair legs to detailed tabletops, ensuring uniformity and quality. Customization is another key benefit, allowing artisans and designers to create unique pieces with consistent accuracy.
Architectural woodworking leverages CNC technology for creating detailed moldings, intricate staircases, and custom doors, enhancing both aesthetics and functionality. This precision extends to joinery, where CNC machines cut precise mortise and tenon joints, dovetails, and other intricate fittings, reducing assembly time and improving structural integrity.
Artistic applications include sculptural woodwork and ornamental carvings, where CNC machines replicate intricate patterns and designs with meticulous detail. This capability extends to signage and decorative panels, catering to both commercial and residential settings.
Prototyping and rapid manufacturing benefit from CNC technology’s ability to quickly iterate designs and produce prototypes with minimal waste. This is crucial in product development and testing phases, allowing for adjustments before full-scale production.
Overall, wood CNC technology combines digital precision with traditional craftsmanship, expanding creative possibilities while improving efficiency and quality in woodworking. Its applications span furniture manufacturing, architectural woodworking, artistic endeavors, and prototyping, making it a versatile tool in modern woodworking industries.
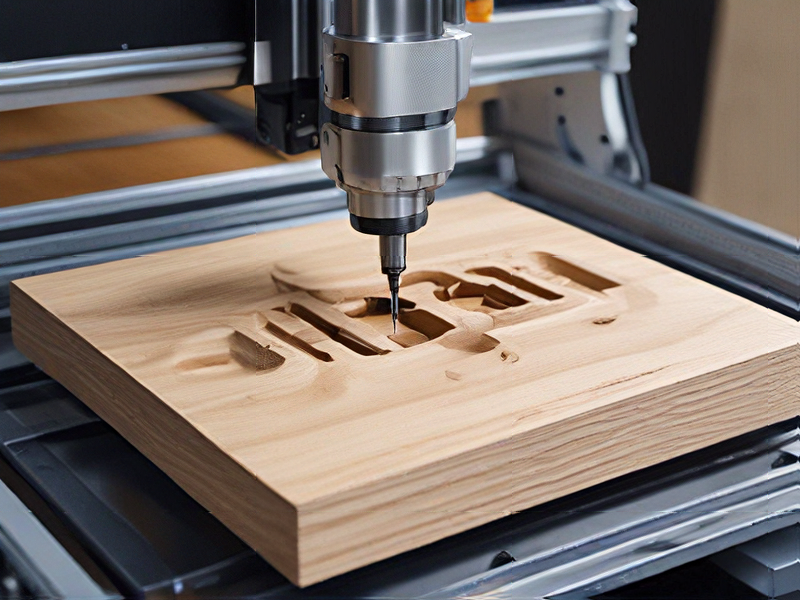
Quality Testing Methods for wood cnc and how to control quality
Quality testing for wood CNC (Computer Numerical Control) involves several methods to ensure precision, durability, and overall product quality. Here are some key methods and how to control quality:
Methods for Quality Testing
1. Dimensional Accuracy Testing:
– Calipers and Micrometers: Measure the dimensions of CNC-cut wood parts to ensure they meet design specifications.
– Coordinate Measuring Machines (CMM): Automated measurement of complex shapes and sizes with high accuracy.
2. Surface Finish Inspection:
– Visual Inspection: Check for any visible defects like burns, splinters, or rough edges.
– Profilometers: Measure surface roughness and texture to ensure a smooth finish.
3. Material Integrity Testing:
– Moisture Content Testing: Use a moisture meter to ensure the wood’s moisture content is within acceptable limits.
– Hardness Testing: Perform tests like the Janka hardness test to verify the wood’s resistance to wear and denting.
4. Functional Testing:
– Assembly Fit: Ensure parts fit together as intended without gaps or misalignments.
– Load Testing: Test the structural integrity by applying stress or load to the parts to ensure durability.
Quality Control Measures
1. Standard Operating Procedures (SOPs):
– Establish detailed SOPs for every stage of the CNC process, from material selection to final inspection, to maintain consistency.
2. Regular Calibration:
– Calibrate CNC machines and measurement tools regularly to ensure accuracy and precision.
3. Quality Management Systems (QMS):
– Implement a QMS like ISO 9001 to maintain systematic quality control processes and continuous improvement.
4. Training and Skill Development:
– Regularly train operators and quality control personnel on the latest techniques and standards in CNC machining and quality testing.
5. Statistical Process Control (SPC):
– Use SPC to monitor and control the CNC process through statistical methods, identifying and correcting deviations in real-time.
By integrating these testing methods and quality control measures, wood CNC operations can consistently produce high-quality products that meet or exceed customer expectations.
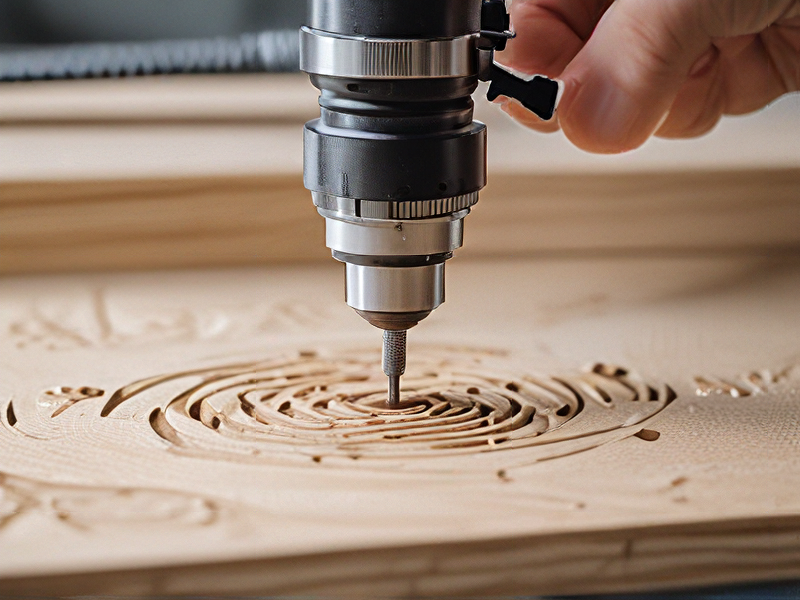
Tips for Procurement and Considerations when Purchasing from wood cnc
When purchasing from wood CNC (Computer Numerical Control) providers, consider these key tips and factors:
1. Machine Specifications: Evaluate the CNC machine’s capabilities such as its cutting area, spindle power, speed, and accuracy. Ensure it meets your production needs and can handle the types of wood and projects you plan to work on.
2. Software Compatibility: Check if the CNC machine is compatible with the design software you use (e.g., CAD/CAM programs). Compatibility ensures seamless workflow from design to production.
3. Build Quality and Durability: Look for machines built from robust materials with solid construction. A durable CNC machine will offer reliability and longevity, reducing maintenance costs over time.
4. Ease of Use and Learning Curve: Consider the user-friendliness of the machine, especially if you’re new to CNC woodworking. Intuitive controls and accessible learning resources can shorten the learning curve and increase productivity.
5. Customer Support and Training: Opt for suppliers that offer comprehensive customer support, including training for operators. Good support ensures you can resolve issues quickly and maximize the machine’s efficiency.
6. Reviews and Reputation: Research customer reviews and testimonials about the CNC provider. A good reputation signifies reliability and customer satisfaction.
7. Cost and Value: Compare prices among different suppliers, but also consider the overall value. A slightly higher initial investment may be worthwhile if the machine offers better performance, reliability, and support.
8. Maintenance Requirements: Understand the maintenance needs of the CNC machine. Regular maintenance ensures optimal performance and extends the machine’s lifespan.
9. Safety Features: Prioritize machines with built-in safety features such as emergency stop buttons, protective enclosures, and automatic tool changers to minimize risks in the workplace.
10. Future Expansion: Anticipate future needs and consider if the machine can be upgraded or expanded with additional features or attachments.
By considering these factors, you can make a well-informed decision when purchasing a CNC machine for woodworking, ensuring it meets your current requirements and supports future growth.
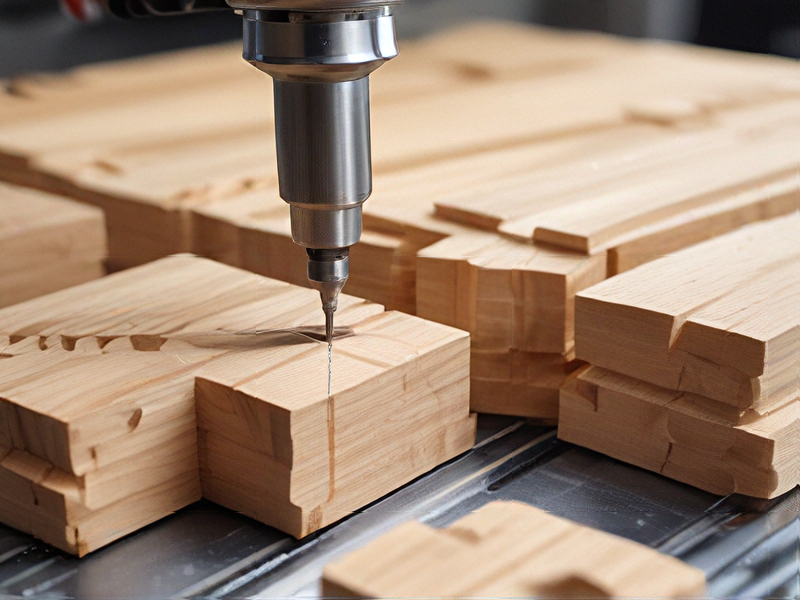
FAQs on Sourcing and Manufacturing from wood cnc in China
FAQs on Sourcing and Manufacturing Wood CNC in China
1. Why source wood CNC machines from China?
China is a leading manufacturer of wood CNC machines due to its advanced technology, skilled labor, and competitive pricing. Chinese manufacturers offer a wide range of models with varying capabilities, making it easier to find machines that fit specific requirements.
2. How to find reliable suppliers?
Use reputable platforms like Alibaba, Made-in-China, and Global Sources. Look for suppliers with good reviews, long operating histories, and verified certifications. Visiting trade shows and requesting samples can also help assess supplier reliability.
3. What certifications should I look for?
Ensure the manufacturer has ISO 9001 certification for quality management. CE certification is crucial if you plan to sell in Europe. Other relevant certifications include UL, RoHS, and FCC, depending on your market.
4. What are the common payment terms?
Typical payment terms include a 30% deposit before production and the remaining 70% before shipment. Some suppliers may offer more flexible terms for large orders or long-term partnerships.
5. How to ensure product quality?
Conduct factory audits, request product samples, and perform pre-shipment inspections. Hiring a third-party quality control firm can provide an unbiased assessment of the machines’ quality.
6. What is the lead time for manufacturing?
Lead times vary but typically range from 30 to 60 days, depending on the machine’s complexity and order size. Custom machines may take longer due to design and testing requirements.
7. Are there any import duties?
Import duties depend on your country’s regulations. Check with local customs authorities to understand the applicable duties and taxes for importing wood CNC machines.
8. How to handle after-sales support?
Choose suppliers offering comprehensive after-sales support, including warranty, spare parts, and technical assistance. Some suppliers provide remote troubleshooting and on-site service for complex issues.
9. What shipping options are available?
Common shipping options include sea freight for large orders and air freight for smaller, urgent shipments. Work with a reliable freight forwarder to manage logistics and ensure timely delivery.
By following these guidelines, you can effectively source and manufacture wood CNC machines from China, ensuring high quality and competitive pricing.
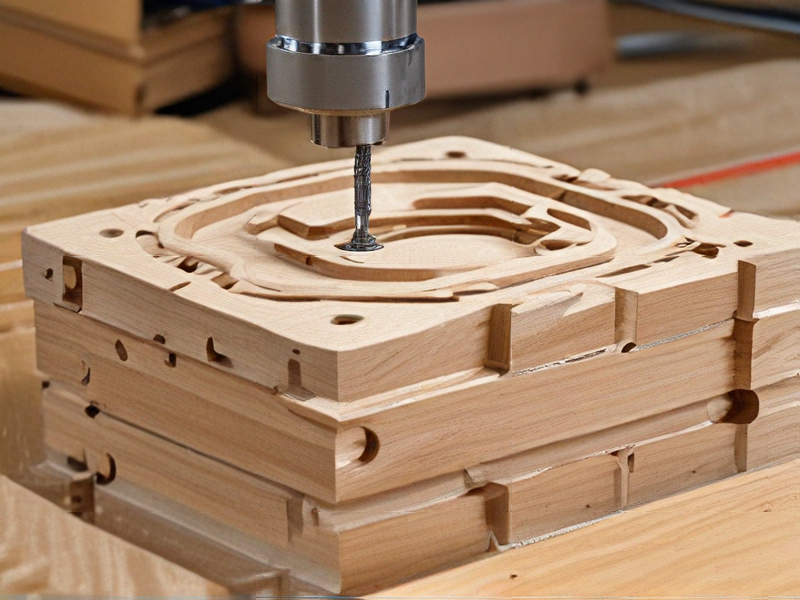