Technology and Applications of wooden cutter machine
A wooden cutter machine, often referred to as a wood cutting machine or wood CNC (Computer Numerical Control) machine, is an essential tool in woodworking. It is designed to cut, shape, and carve wood with precision and efficiency, significantly enhancing productivity in both industrial and hobbyist woodworking.
Technology
Modern wooden cutter machines incorporate advanced technologies such as CNC, laser cutting, and automated control systems. CNC technology allows for precise control over the cutting process through computer programming, enabling complex designs and intricate patterns to be cut with high accuracy. Laser cutting technology uses a focused laser beam to cut through wood, providing clean and precise edges without physical contact. Automated control systems enhance operational efficiency and safety by allowing for programmable and repeatable cutting actions.
Applications
1. Furniture Manufacturing: Wooden cutter machines are extensively used in the production of furniture, enabling the mass production of components with high precision and consistency. This includes cutting and shaping parts for tables, chairs, cabinets, and more.
2. Carpentry and Joinery: These machines aid in creating detailed joinery, intricate designs, and custom woodworking projects. They are essential for producing doors, window frames, moldings, and other architectural elements.
3. Art and Craft: Wood CNC machines allow artists and craftsmen to create detailed sculptures, engravings, and decorative items. The precision of CNC technology facilitates the creation of complex patterns and fine details that would be challenging to achieve manually.
4. Prototyping and Model Making: In industries like architecture and engineering, wooden cutter machines are used for creating scale models and prototypes. This helps in visualizing and testing designs before full-scale production.
5. Signage: Wood cutting machines are also employed in the production of wooden signs and displays, providing a high level of detail and customizability.
Conclusion
The integration of advanced technologies in wooden cutter machines has revolutionized woodworking, providing high precision, efficiency, and versatility. These machines are indispensable across various sectors, including furniture manufacturing, carpentry, art, and industrial prototyping, showcasing their wide-ranging applications and benefits.
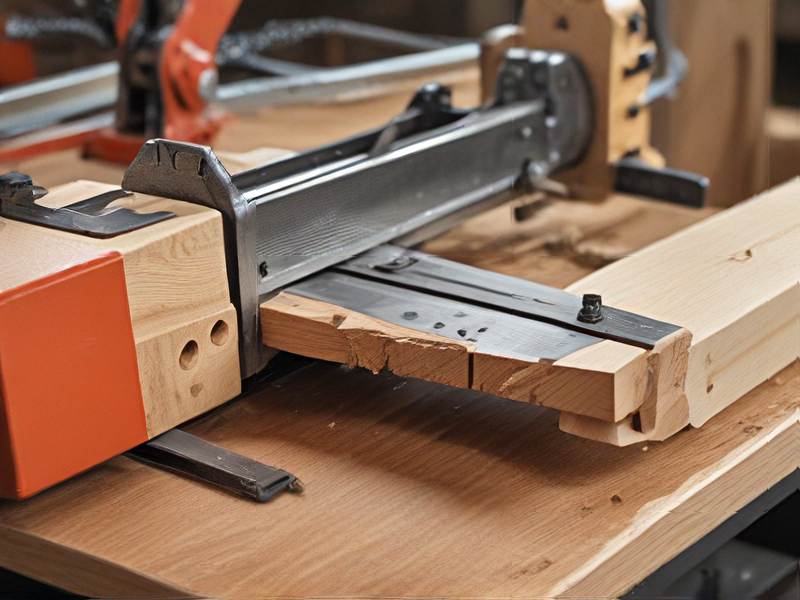
Quality Testing Methods for wooden cutter machine and how to control quality
Quality Testing Methods for Wooden Cutter Machines
1. Dimensional Accuracy: Verify the precision of cuts by measuring the dimensions of cut wood against specified tolerances using calipers and micrometers.
2. Cut Surface Quality: Inspect the smoothness and finish of the cut surfaces. Use visual inspections and surface roughness testers to ensure the absence of splinters, burns, or uneven edges.
3. Operational Tests: Conduct operational tests to evaluate machine performance under different loads and speeds. This includes checking for consistent cutting speed, feed rate, and power consumption.
4. Durability Testing: Assess the machine’s durability by running it continuously over extended periods and under varying conditions to identify any signs of wear or mechanical failure.
5. Safety Checks: Ensure all safety features such as emergency stops, guards, and sensors are functioning correctly. Perform regular safety audits and simulations of emergency scenarios.
6. Noise and Vibration Analysis: Measure the noise levels and vibrations using decibel meters and vibration analyzers. Machines should operate within acceptable noise and vibration thresholds to prevent operator fatigue and damage to the machine.
Quality Control Measures
1. Standard Operating Procedures (SOPs): Implement detailed SOPs for machine operation, maintenance, and quality checks. Ensure all operators are trained and adhere to these procedures.
2. Regular Maintenance Schedules: Establish and follow a strict maintenance schedule, including routine inspections, lubrication, and replacement of worn-out parts to prevent breakdowns and maintain optimal performance.
3. Calibration: Regularly calibrate measuring instruments and machine settings to ensure accuracy. Use standard reference materials for calibration.
4. Statistical Process Control (SPC): Utilize SPC techniques to monitor and control the machining process. Track key performance indicators (KPIs) and analyze data to identify and rectify deviations from quality standards.
5. Documentation and Traceability: Maintain thorough records of all quality tests, maintenance activities, and machine performance. This ensures traceability and aids in identifying recurring issues.
6. Continuous Improvement: Foster a culture of continuous improvement by regularly reviewing and updating quality control procedures based on feedback and technological advancements.
By combining these testing methods and control measures, the quality of wooden cutter machines can be effectively managed, ensuring reliability and precision in their operation.
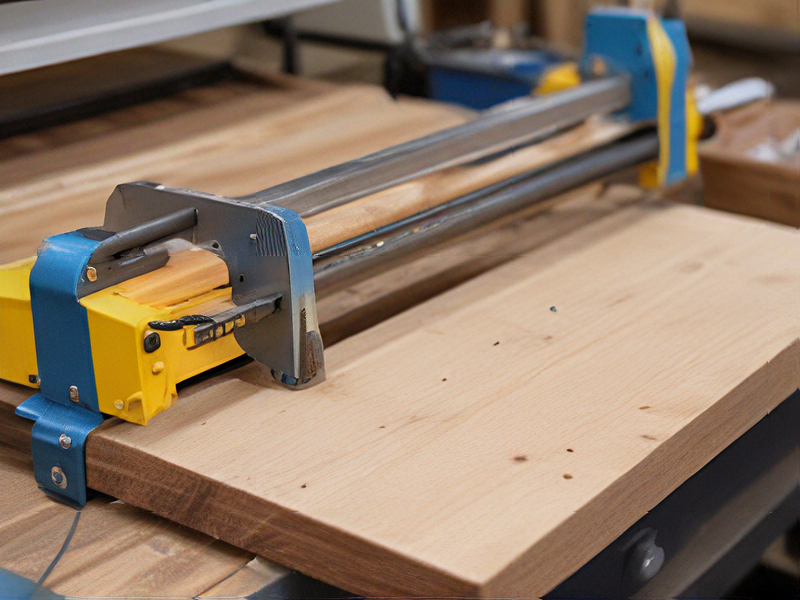
Tips for Procurement and Considerations when Purchasing from wooden cutter machine
When procuring a wooden cutter machine, consider these essential tips and factors:
1. Machine Specifications: Evaluate the machine’s cutting capacity, speed, and compatibility with different types of wood. Ensure it meets your production needs without compromising on quality.
2. Durability and Build Quality: Look for machines built with robust materials that can withstand the demands of continuous use. Check reviews and warranties to gauge reliability.
3. Safety Features: Prioritize machines equipped with safety guards, emergency stop buttons, and automatic braking systems to minimize the risk of accidents.
4. Ease of Use and Maintenance: Opt for machines that are user-friendly with intuitive controls. Easy maintenance procedures and access to spare parts are crucial for minimizing downtime.
5. Supplier Reputation: Choose a reputable supplier with a track record of delivering quality products and excellent customer support. Read customer reviews and ask for references if necessary.
6. Cost and ROI: Consider not only the upfront cost but also the long-term return on investment (ROI). A higher initial investment may be justified if it leads to increased productivity and reduced operational costs over time.
7. Training and Support: Ensure the supplier offers adequate training for your operators. Good technical support and availability of manuals/documentation are also important.
8. Compatibility with Existing Systems: If integrating with existing production lines, ensure compatibility with other equipment and software.
9. Environmental Impact: Assess the machine’s energy efficiency and environmental impact. Look for certifications or compliance with industry standards.
10. Future Expansion: Consider scalability if you anticipate increasing production capacity in the future. Choose a machine that can grow with your business.
By carefully considering these factors and conducting thorough research, you can make an informed decision when purchasing a wooden cutter machine that aligns with your operational requirements and business goals.
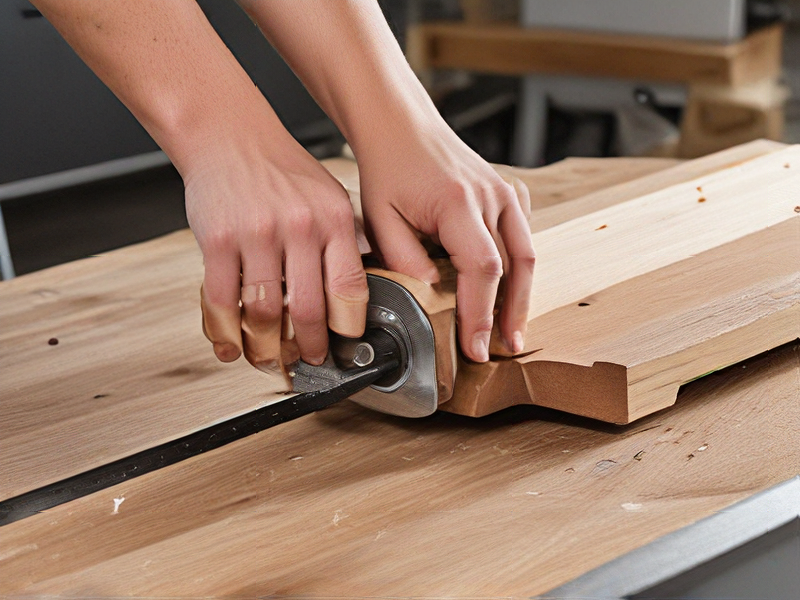
FAQs on Sourcing and Manufacturing from wooden cutter machine in China
FAQs on Sourcing and Manufacturing Wooden Cutter Machines in China
1. Why source wooden cutter machines from China?
China is a global leader in manufacturing, offering competitive prices, advanced technology, and a wide range of suppliers. The large-scale production and skilled workforce ensure high-quality products at lower costs.
2. How to find reliable suppliers?
Utilize platforms like Alibaba, Made-in-China, and Global Sources. Attend trade shows like Canton Fair. Verify suppliers through reviews, certifications, and factory visits. Third-party inspection services can also help.
3. What are the key considerations when choosing a supplier?
Check the supplier’s manufacturing capacity, product quality, certifications (ISO, CE), and customer service. Evaluate their experience, communication skills, and willingness to provide samples.
4. How can I ensure product quality?
Request samples before placing bulk orders. Conduct factory audits and use third-party inspection services. Ensure the supplier adheres to international standards and provides warranties.
5. What are the common payment terms?
Common terms include Telegraphic Transfer (T/T), Letter of Credit (L/C), and Western Union. A typical structure might be 30% upfront and 70% upon shipment or after inspection.
6. What about shipping and logistics?
Work with reputable freight forwarders. Choose between sea, air, or rail depending on urgency and budget. Ensure proper packaging to prevent damage. Understand Incoterms (FOB, CIF) to know who is responsible for what part of the shipping process.
7. Are there any import regulations?
Research and comply with your country’s import regulations. This includes tariffs, duties, and necessary certifications. Working with a customs broker can simplify this process.
8. How to handle after-sales service and spare parts?
Clarify warranty terms and availability of spare parts beforehand. Some suppliers offer training, technical support, and maintenance services.
9. What are the potential risks and how to mitigate them?
Risks include quality issues, delays, and communication barriers. Mitigate these by thorough vetting, clear contracts, regular communication, and possibly having a local agent.
10. How to build a long-term relationship with suppliers?
Maintain regular communication, provide feedback, and pay on time. Visiting suppliers and building personal relationships can also enhance trust and cooperation.
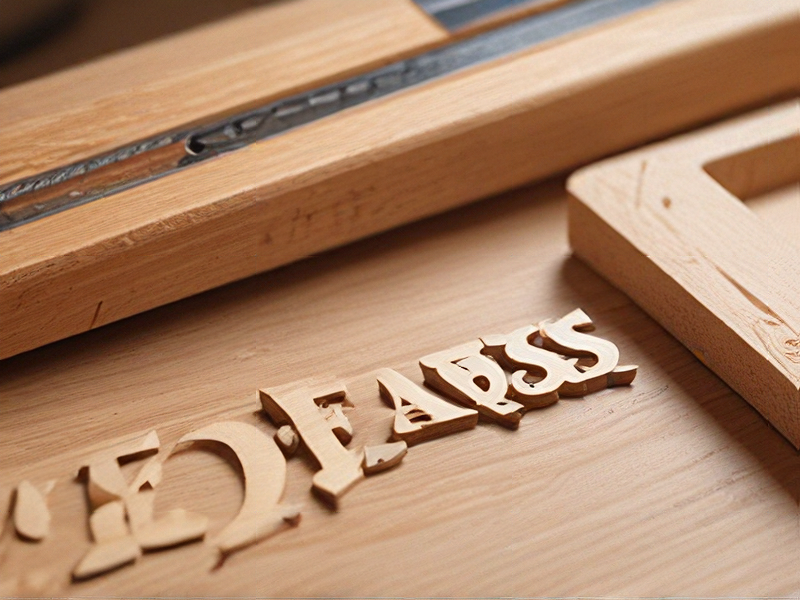