Technology and Applications of woodworking carving machine
Woodworking carving machines encompass a range of technologies designed to automate and enhance the process of carving wood, catering to both industrial and artisanal applications. These machines typically utilize computer numerical control (CNC) technology, which allows for precise and repeatable carving operations based on digital designs.
Key technologies integrated into these machines include:
1. CNC Control: CNC systems drive the carving machine based on digital models, ensuring high precision and complex detailing that would be challenging to achieve manually.
2. Rotary Tools: These machines often feature rotary cutting tools such as routers and spindle cutters. These tools can vary in size and speed, enabling different types of cuts and finishes.
3. CAD/CAM Software: Computer-aided design (CAD) and computer-aided manufacturing (CAM) software are essential for creating designs and converting them into toolpaths that the CNC machine can follow. This software allows for intricate and customized designs to be translated into physical carvings.
4. Material Handling Systems: Some advanced machines incorporate automated material handling systems that can feed and position wood blanks or workpieces, optimizing workflow efficiency.
Applications of woodworking carving machines span various industries:
– Furniture Manufacturing: Used for carving intricate designs on furniture components, adding decorative elements to chairs, tables, and cabinets.
– Art and Sculpture: Artists and sculptors utilize these machines to create detailed sculptures and art pieces with consistent quality.
– Architectural Millwork: Carving ornate details for architectural elements like moldings, panels, and doors.
– Sign Making and Woodcraft: Producing custom signs, plaques, and personalized woodcraft items with intricate designs.
Overall, woodworking carving machines combine advanced technology with traditional craftsmanship, enabling precise, efficient, and customizable wood carving solutions across diverse applications. Their ability to replicate designs faithfully and handle complex patterns makes them indispensable tools in modern woodworking industries.
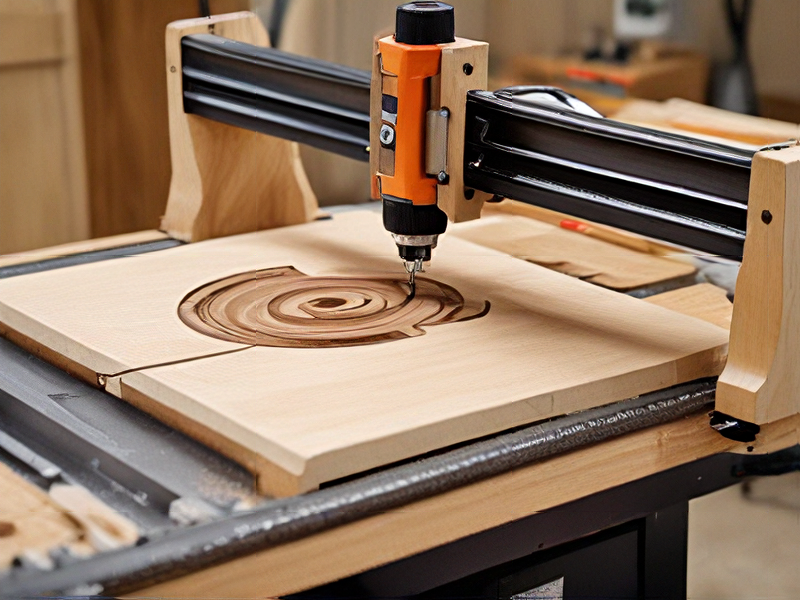
Quality Testing Methods for woodworking carving machine and how to control quality
To ensure quality in woodworking carving machines, several testing methods can be employed:
1. Dimensional Accuracy Checks: Use precision measuring tools to verify dimensions of carved products against specifications.
2. Surface Quality Inspection: Visual and tactile inspection for smoothness, uniformity, and absence of defects like tear-outs or splinters.
3. Material Strength Testing: Assess the durability and strength of carved materials through stress tests or load-bearing trials.
4. Accuracy of Carving Patterns: Verify the fidelity of carved patterns to digital designs using digital imaging or template overlays.
5. Operational Performance Testing: Run the machine through its operational cycles to check for consistent performance and reliability.
Controlling quality involves implementing the following measures:
1. Standard Operating Procedures (SOPs): Documented procedures for setup, operation, and maintenance to ensure consistency.
2. Regular Maintenance: Scheduled checks and servicing to prevent breakdowns and maintain performance.
3. Training and Skill Development: Ensure operators are trained to operate machines effectively and identify quality issues.
4. Quality Control Points: Integrate checkpoints throughout production to catch defects early.
5. Feedback Loops: Collect feedback from operators and customers to continuously improve processes.
By employing these methods and controls, woodworking carving machine manufacturers can maintain high-quality standards and minimize defects in their products.
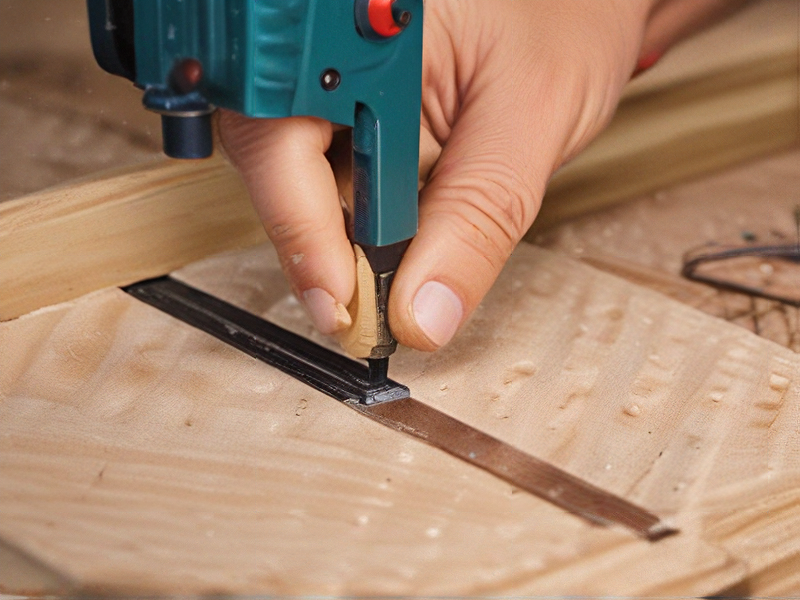
Tips for Procurement and Considerations when Purchasing from woodworking carving machine
When purchasing a woodworking carving machine, consider these key tips for procurement:
1. Machine Specifications: Evaluate the machine’s capabilities such as carving dimensions, spindle power, speed, and compatibility with different materials (wood types).
2. Accuracy and Precision: Look for machines that offer high accuracy in carving intricate designs. Check for reviews or demonstrations showcasing precision.
3. Ease of Use: Choose a machine with a user-friendly interface and intuitive controls. Training requirements for operators should also be considered.
4. Maintenance Requirements: Assess maintenance needs such as lubrication, tool changes, and overall upkeep. Machines with easy maintenance routines can reduce downtime.
5. Manufacturer Support: Opt for machines from reputable manufacturers known for quality products and reliable customer support. Warranty coverage and technical assistance are crucial.
6. Safety Features: Prioritize machines with robust safety features like emergency stop buttons, protective enclosures, and user training materials on safe operation.
7. Cost and ROI: Compare initial purchase costs with long-term benefits and return on investment (ROI). Factor in operational costs like power consumption and tooling expenses.
8. Compatibility with Software: Ensure compatibility with your preferred design software for creating and importing carving patterns.
9. Reviews and References: Read customer reviews and seek references from other woodworking professionals to gauge real-world performance and reliability.
10. Future Expansion: Consider scalability if your business plans include expanding production capabilities or diversifying into different types of woodworking projects.
By focusing on these considerations, you can make an informed decision when purchasing a woodworking carving machine that meets your operational needs and enhances productivity in your woodworking endeavors.
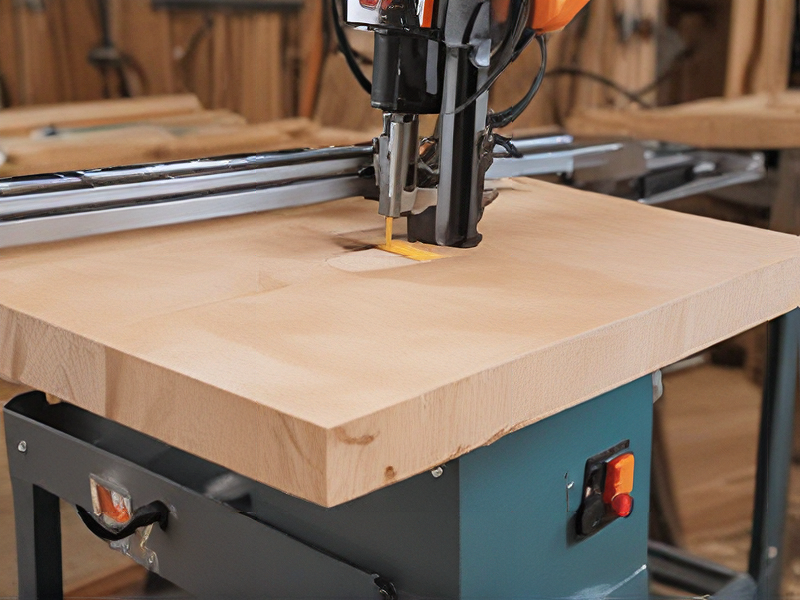
FAQs on Sourcing and Manufacturing from woodworking carving machine in China
When sourcing woodworking carving machines from China, several FAQs often arise:
1. Quality Assurance: Ensure the manufacturer adheres to international quality standards (e.g., ISO certifications) and inquire about their quality control processes.
2. Customization: Check if the manufacturer can customize machines to suit specific requirements, including voltage compatibility and additional features.
3. Lead Times: Clarify production lead times, including manufacturing, testing, and shipping durations to plan inventory and project timelines effectively.
4. MOQ and Pricing: Understand minimum order quantities (MOQs) and negotiate pricing based on order volume and machine specifications.
5. Logistics and Shipping: Discuss logistics arrangements, shipping methods, and responsibilities for customs clearance to manage costs and timelines.
6. After-Sales Support: Inquire about warranty periods, technical support availability, and spare parts accessibility to ensure ongoing machine reliability.
7. Payment Terms: Clarify payment terms such as deposits, milestone payments, and final balance settlement to align with financial planning.
8. Communication: Establish clear lines of communication, preferably with a dedicated account manager fluent in English, to address inquiries promptly.
9. References and Reviews: Request references from past clients or check online reviews to gauge the manufacturer’s reputation and reliability.
10. Intellectual Property: Discuss intellectual property protection measures to safeguard designs and innovations during and after production.
By addressing these FAQs early in the sourcing process, businesses can mitigate risks, ensure product quality, and establish a reliable partnership with Chinese manufacturers for woodworking carving machines.
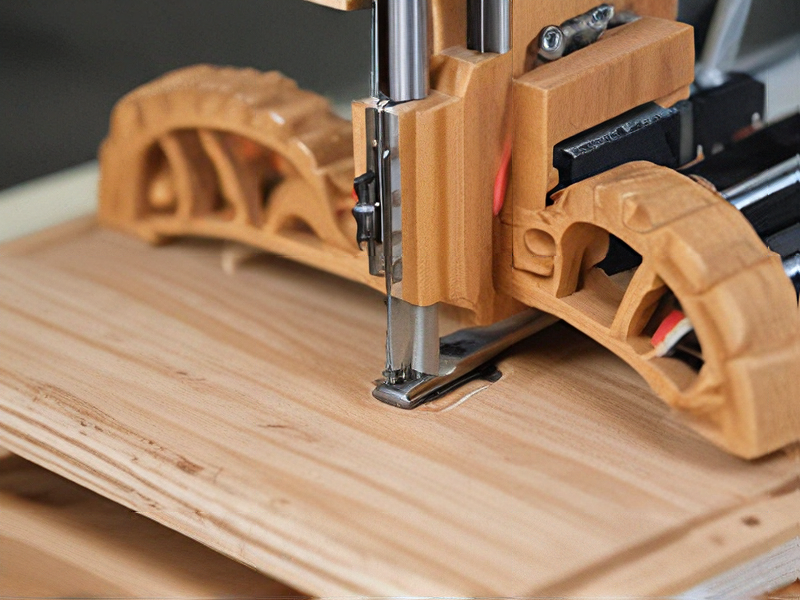